Hello everyone, today I have another board on my desk which I purchased as “working” but while my board boots up, it has issues.
Irem produced several models of motherboards, and this motherboard is M92. It is a 2-stack board, consisting of a motherboard and a ROM board. M92 does not have any schematics.
[Editor Note: wickerwacka produced some partial schematics of the M92 when implementing his FPGA core. Also take a look at our Irem M92 entry in PCB Encyclopedia]
First let’s take a look at our board.
Main board:
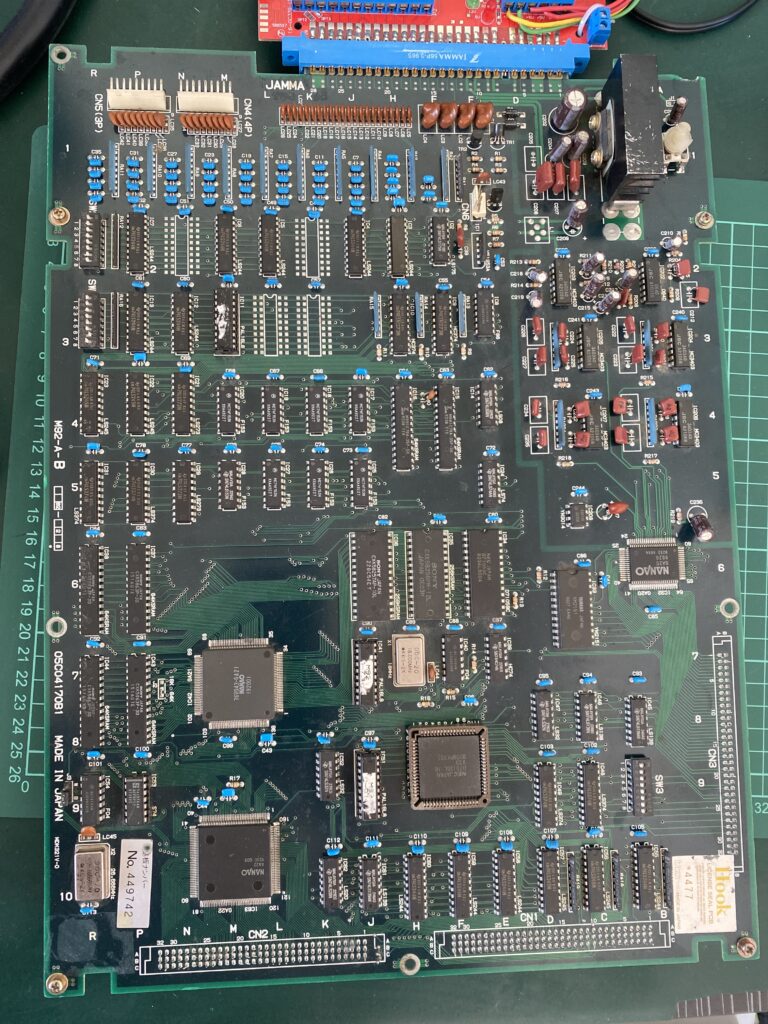
ROM Board
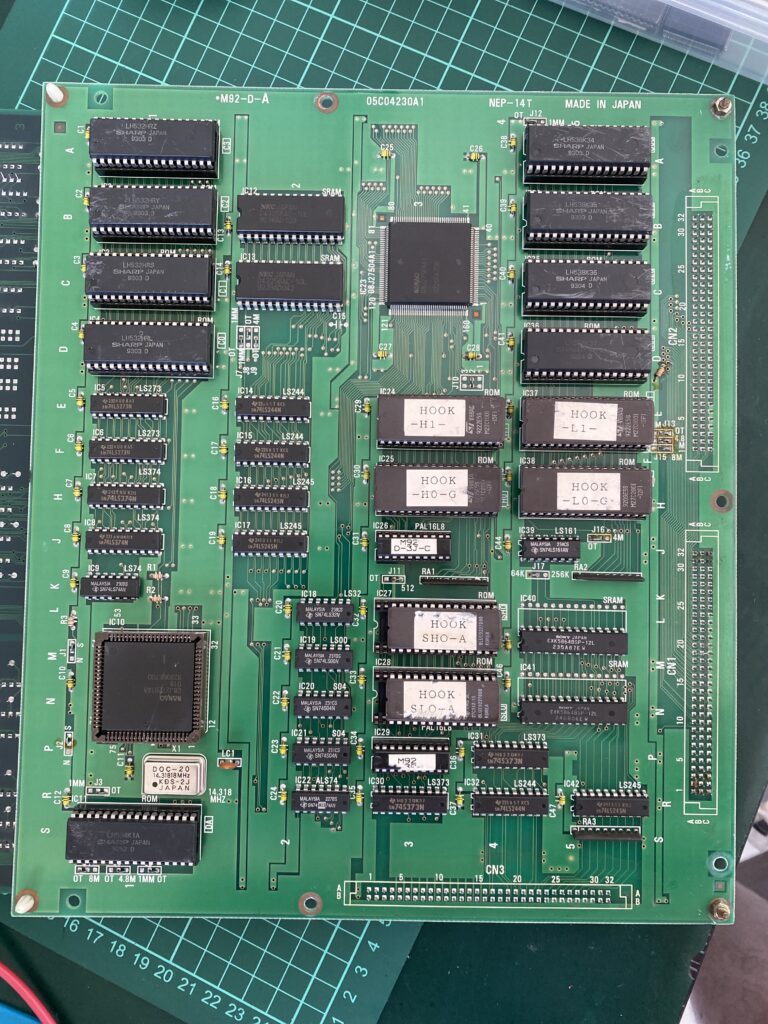
When I power up the board, it passes the RAM and ROM test successfully.
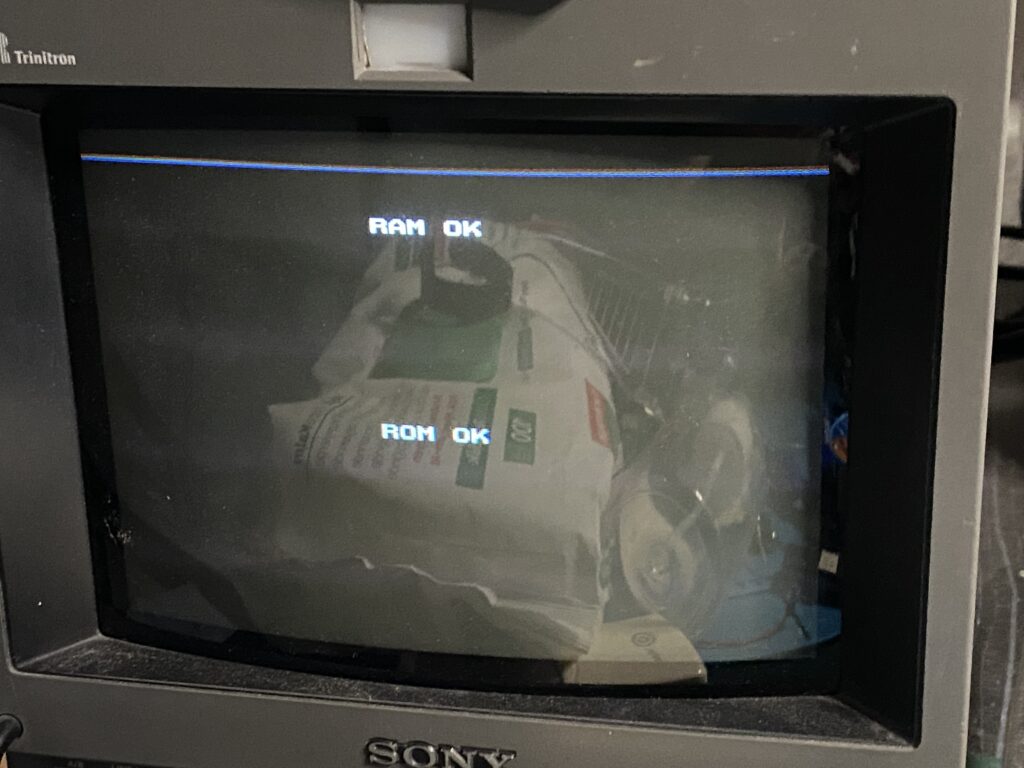
However, in the warning text, you will see a line at the bottom of the screen. That’s one of our problems.
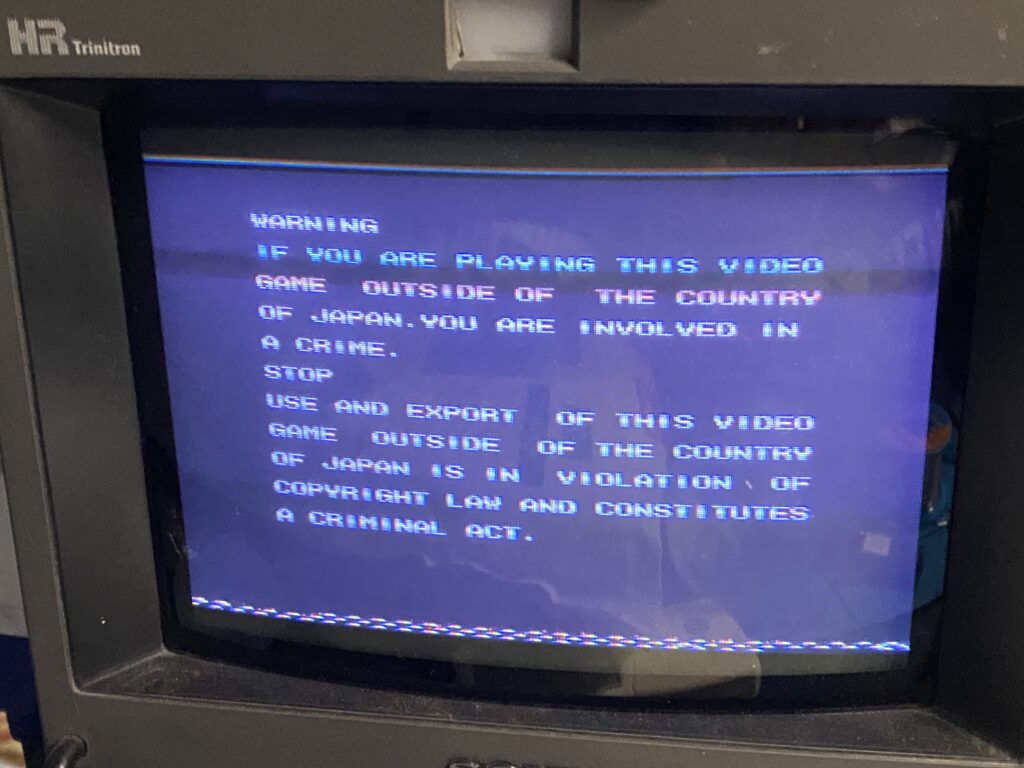
Here you can see another problem, there is a vertical line on the left and right of the screen.
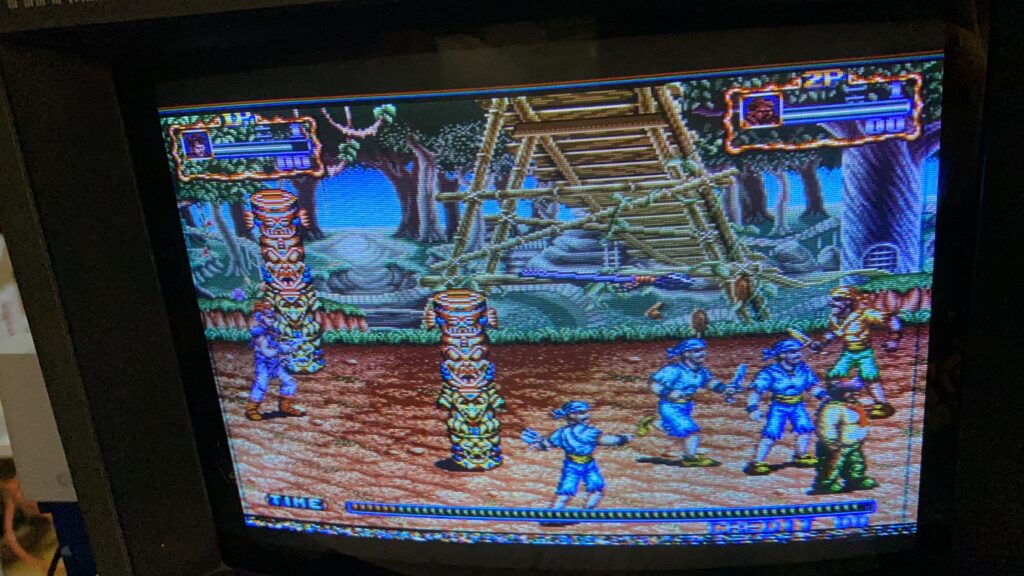
These are the most obvious problems. It is difficult to show the real problem with a photo. Take a look at this video of the problem:
As you can see, as our character moves forward and the background changes, there are flashes and/or color changes on the screen. This is our biggest problem.
Let’s do a physical inspection. The ROM board seems clean and problem-free enough. I move on to the motherboard.
The mainboard has been worked on before – one of the chips has been changed or reflowed.
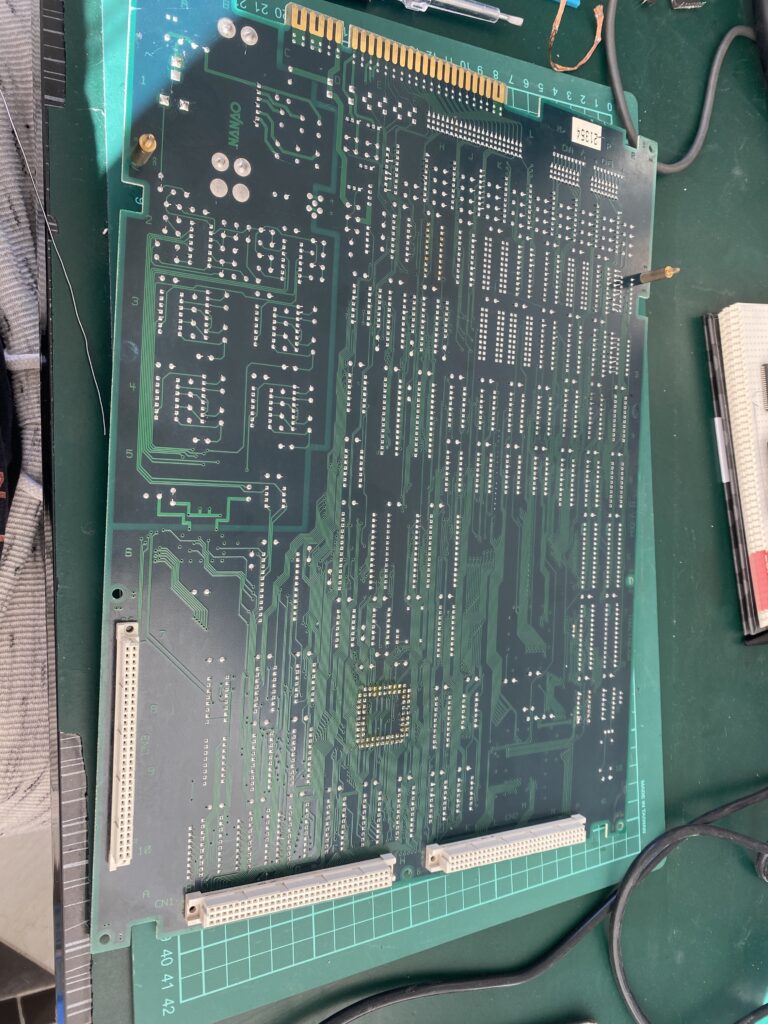
When I look closer, I see a solder bridge. This bridge belongs to 74LS74AN part.
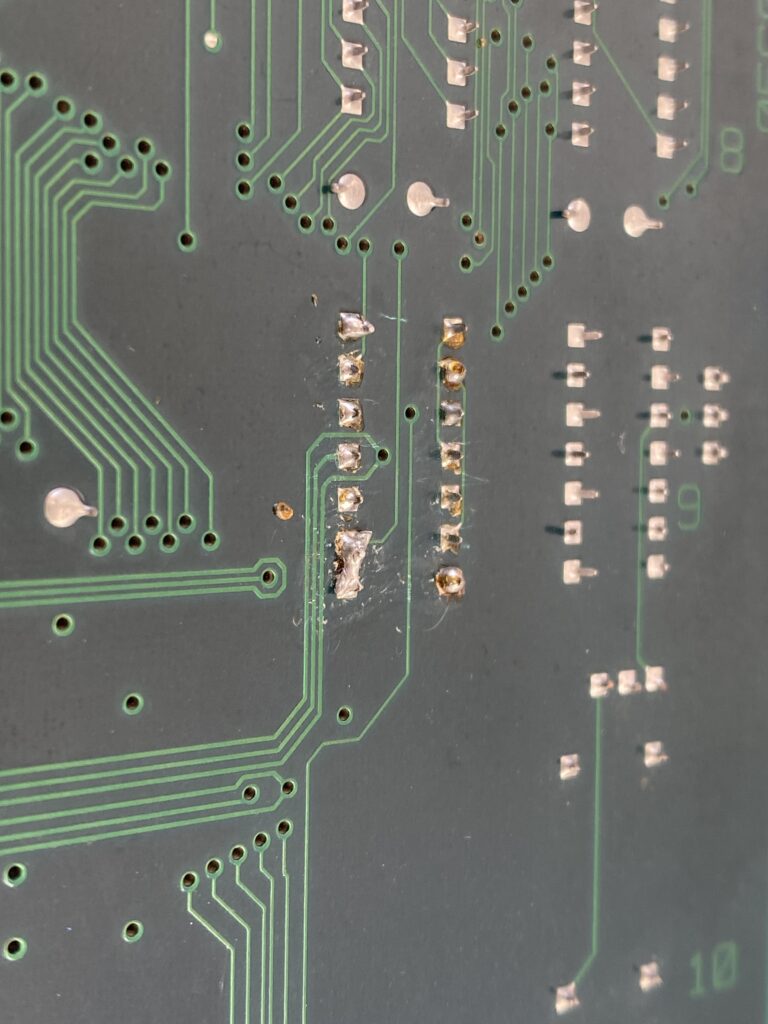
I separate the bridge with a tiny touch of a soldering iron.

But removing this bridge causes no change with the game.
Next, I keep the game on for about half an hour, then I check the chips one by one to see if any of them are overheating. It seems that three of the ICs on the ROM board, which I have highlighted in blue, are overheating.
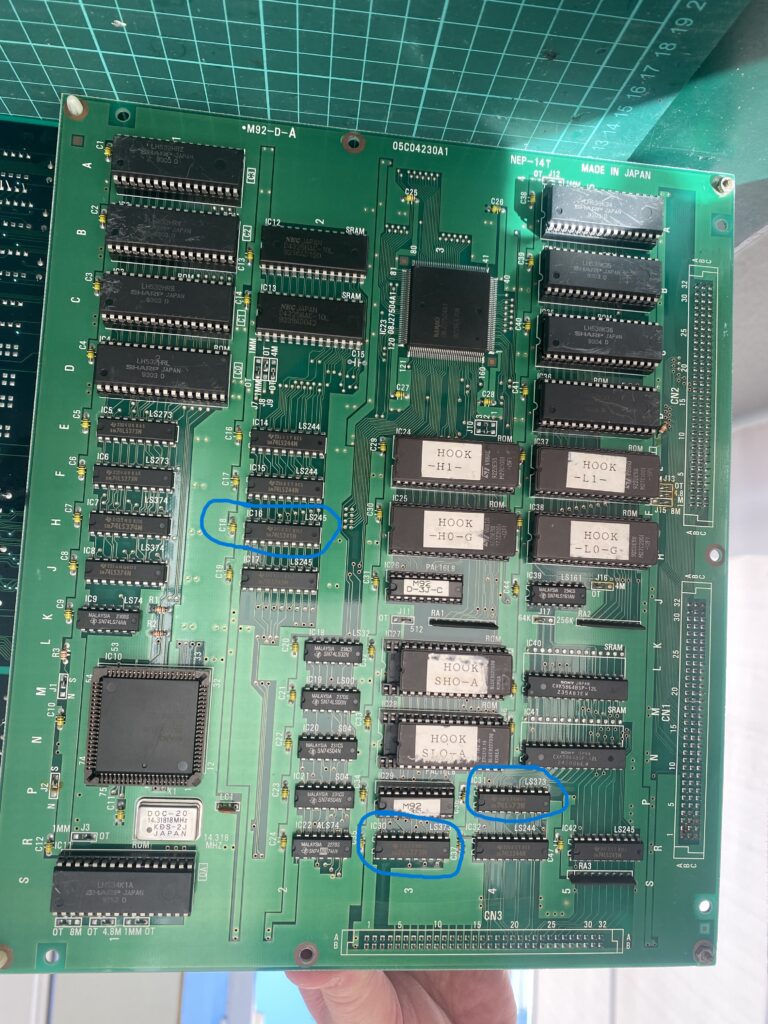
One by one, I remove the parts and test them out of circuit with my EPROM programmer. One of the SN74S373N parts fails the test.
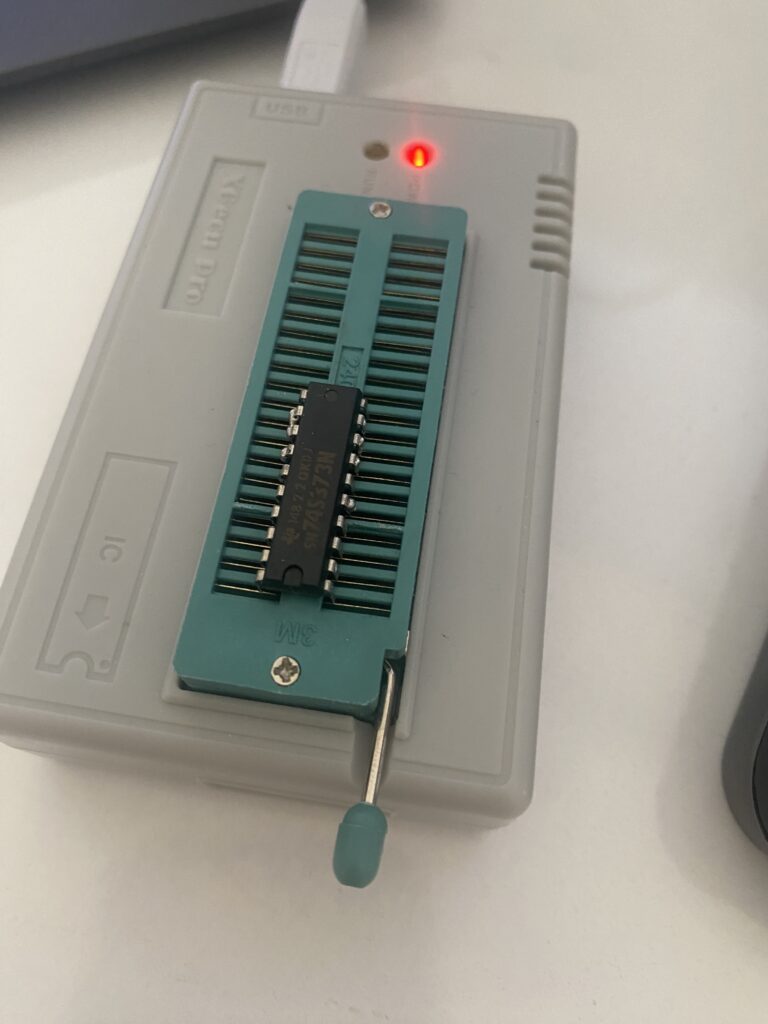
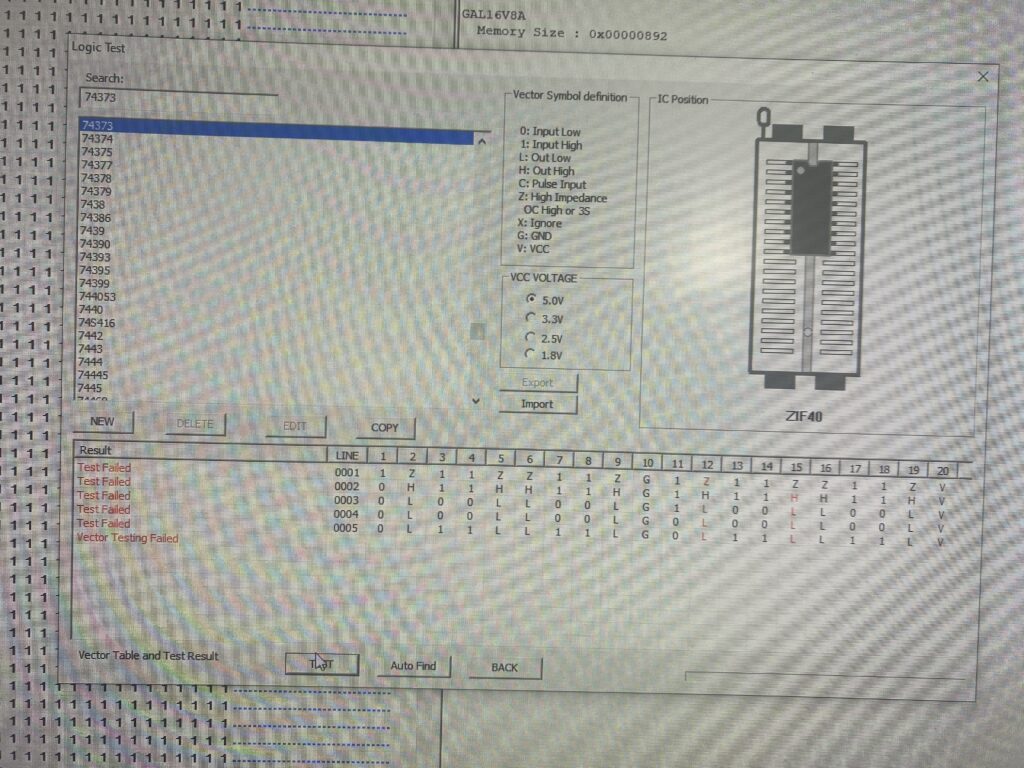
I install socket and replace all three parts.
IC18
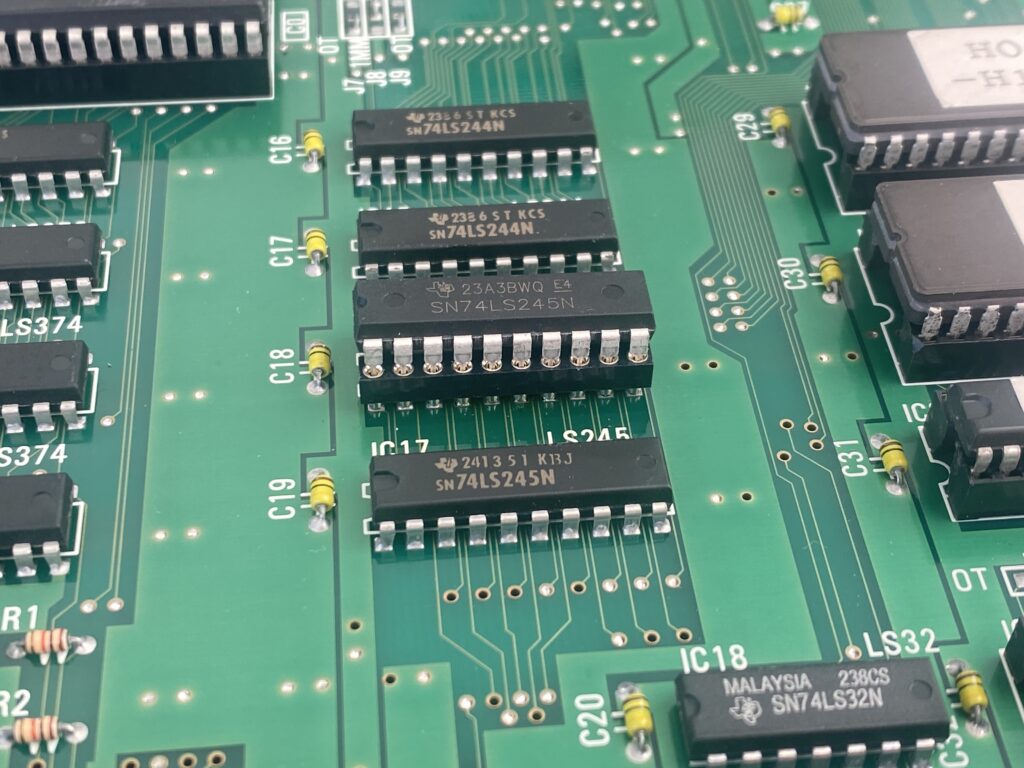
IC30 and IC31
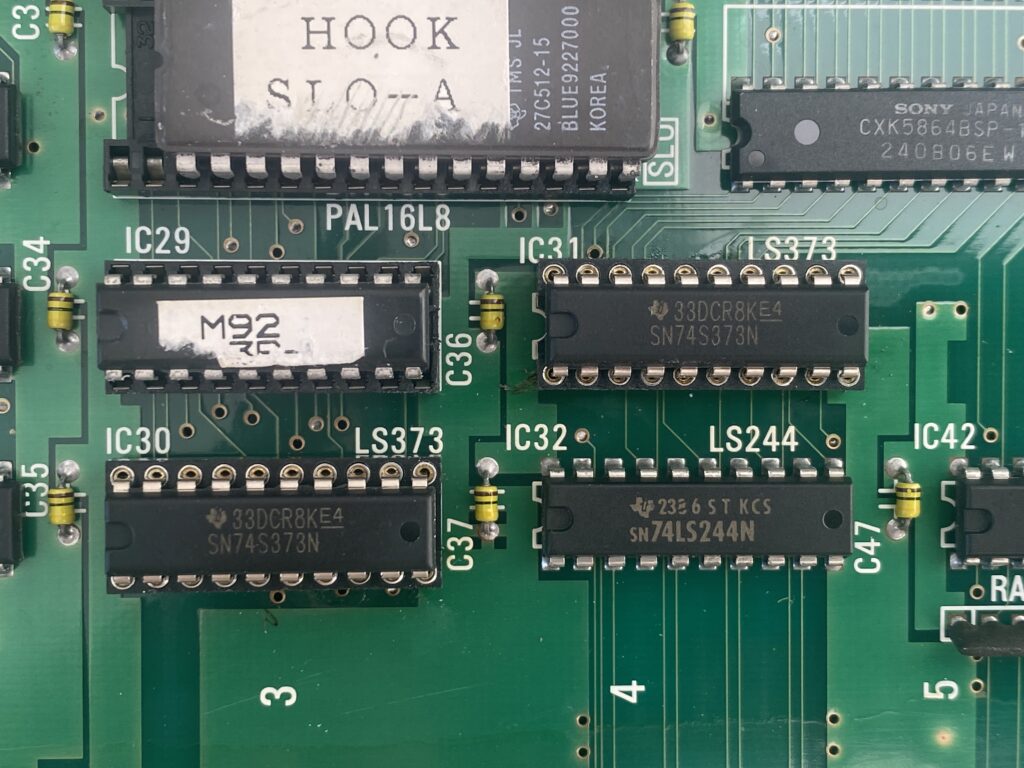
Unfortunately, there’s no change in the game – but there’s no more overheating chips now either.
The next task is to check the ROMs by dumping them and comparing the dumps with MAME. I remove everything from the ROM board (both for cleaning and to check the ROMs)
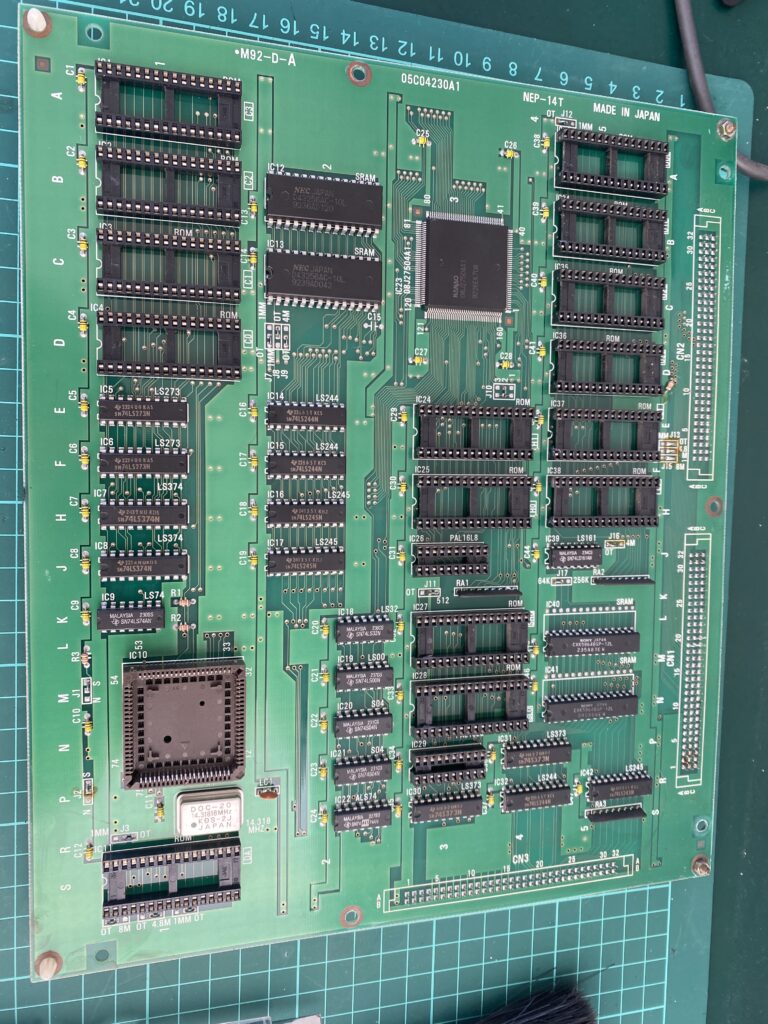
I set the chips down on a notebook in the same order so I don’t forget their places.
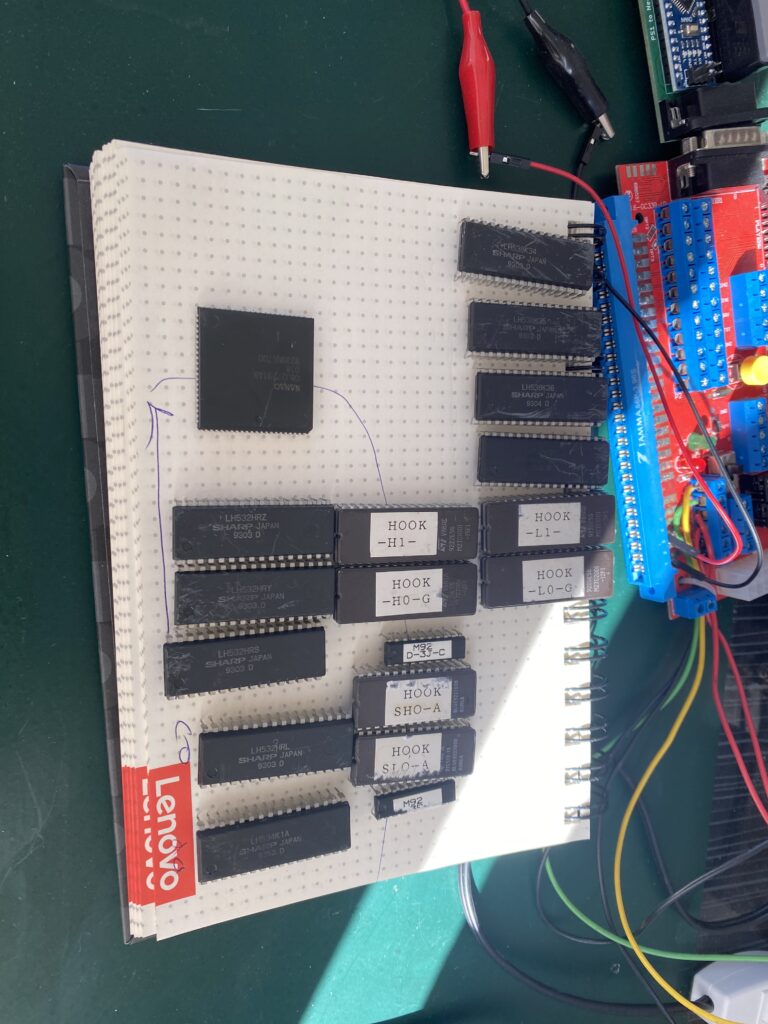
When dumping the ROMs, if it is not written on the chip you are reading what type of part it is, we either check MAME or we look for solutions in forums.
[Editor Note: the part numbers for ROMs with Irem M92 boards are in our PCB Encyclopedia]
There were 3 types of ROMs on this board. Let me specify how to read them:
532 –> 27C020
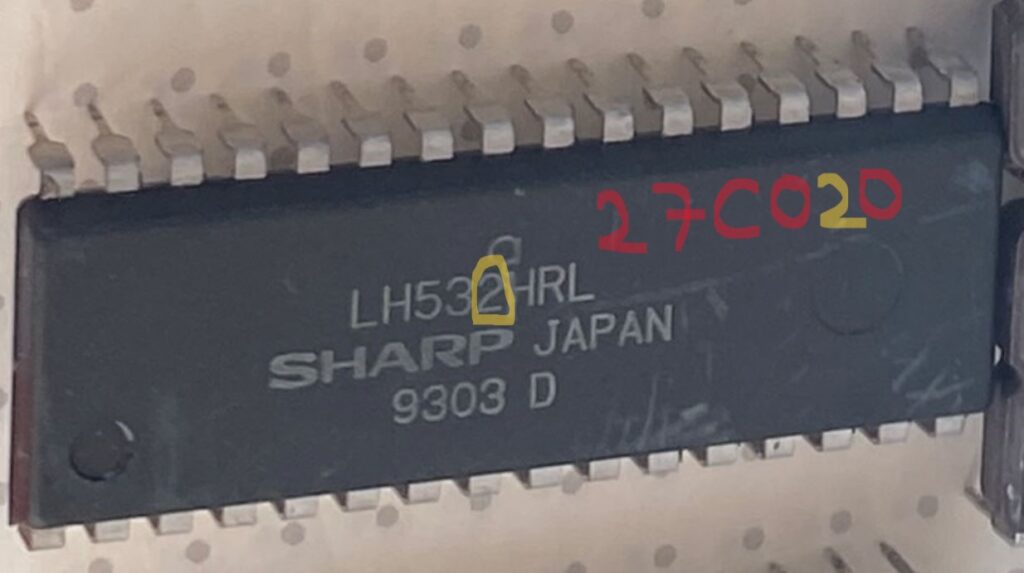
534 –> 27C040
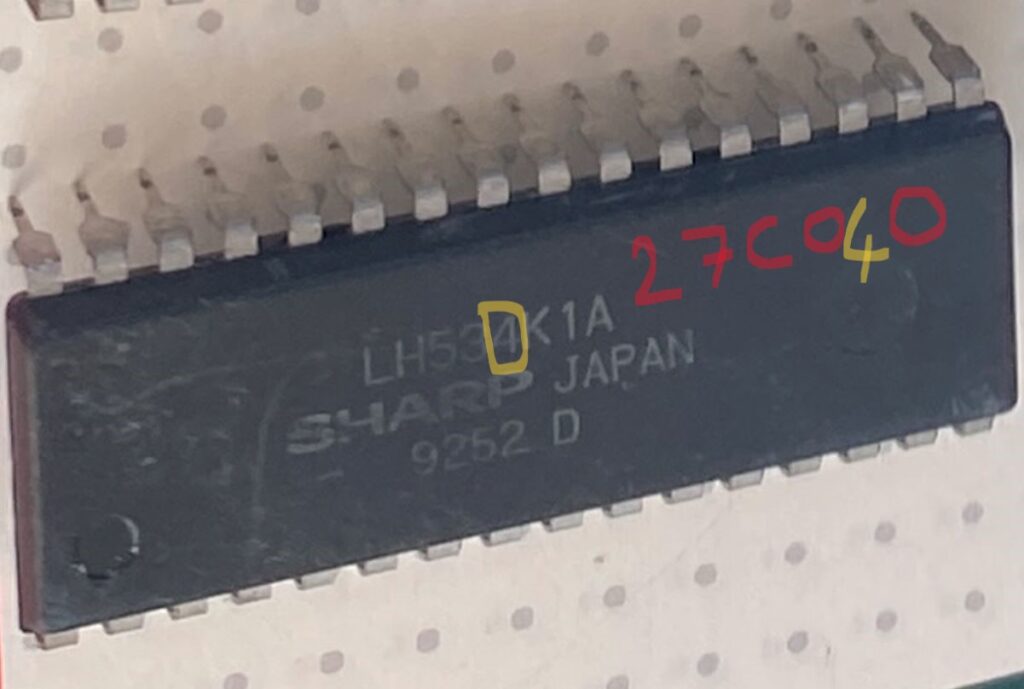
538 –> 27C080
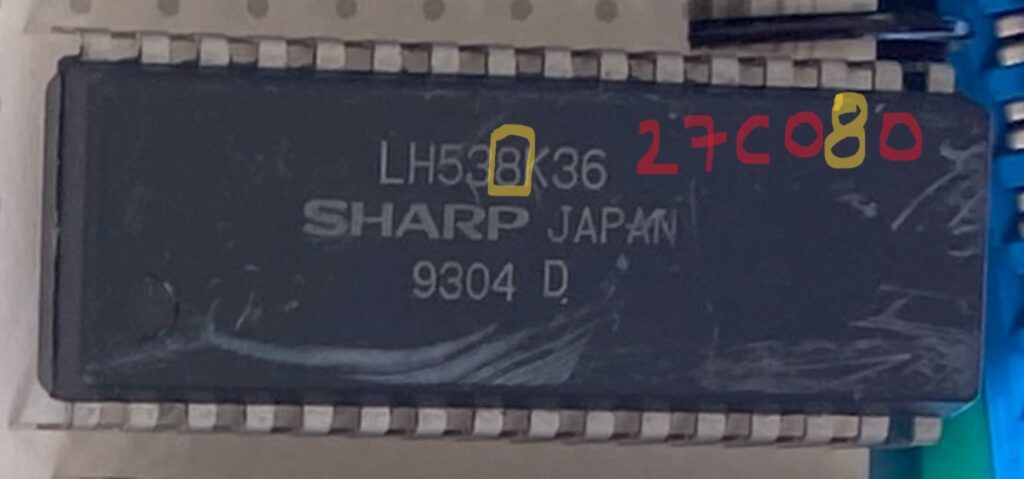
After dumping the ROMs and comparing them, it seems that most of them are okay.
L0
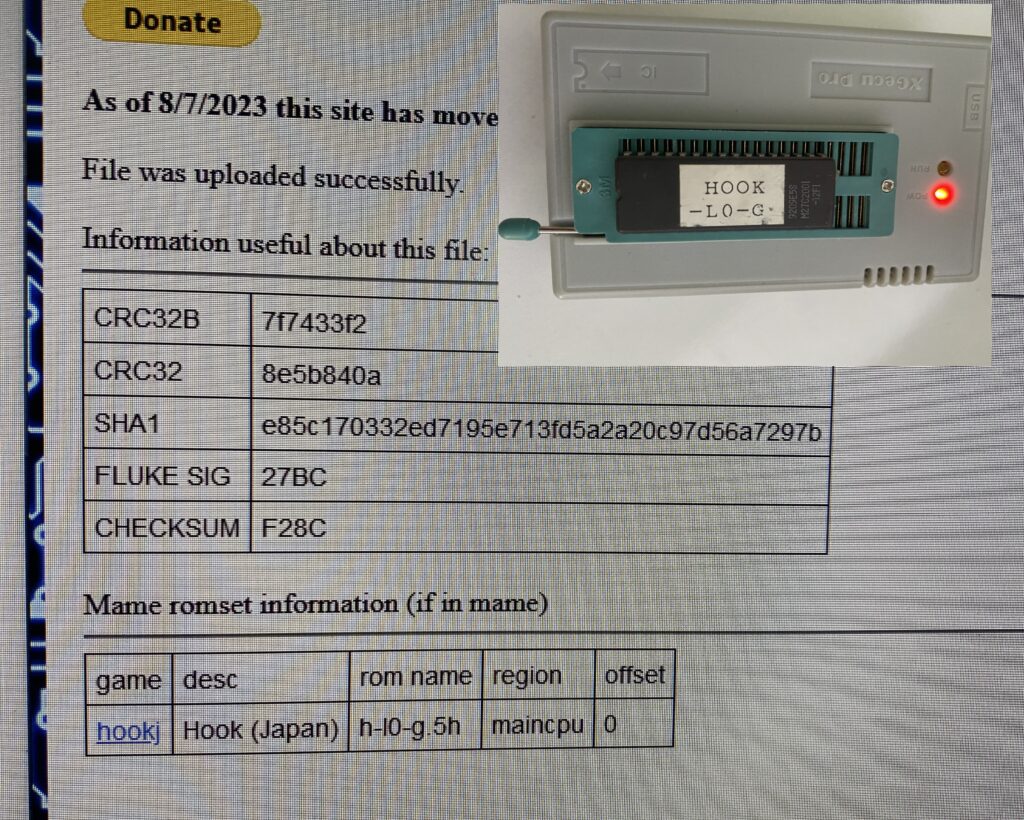
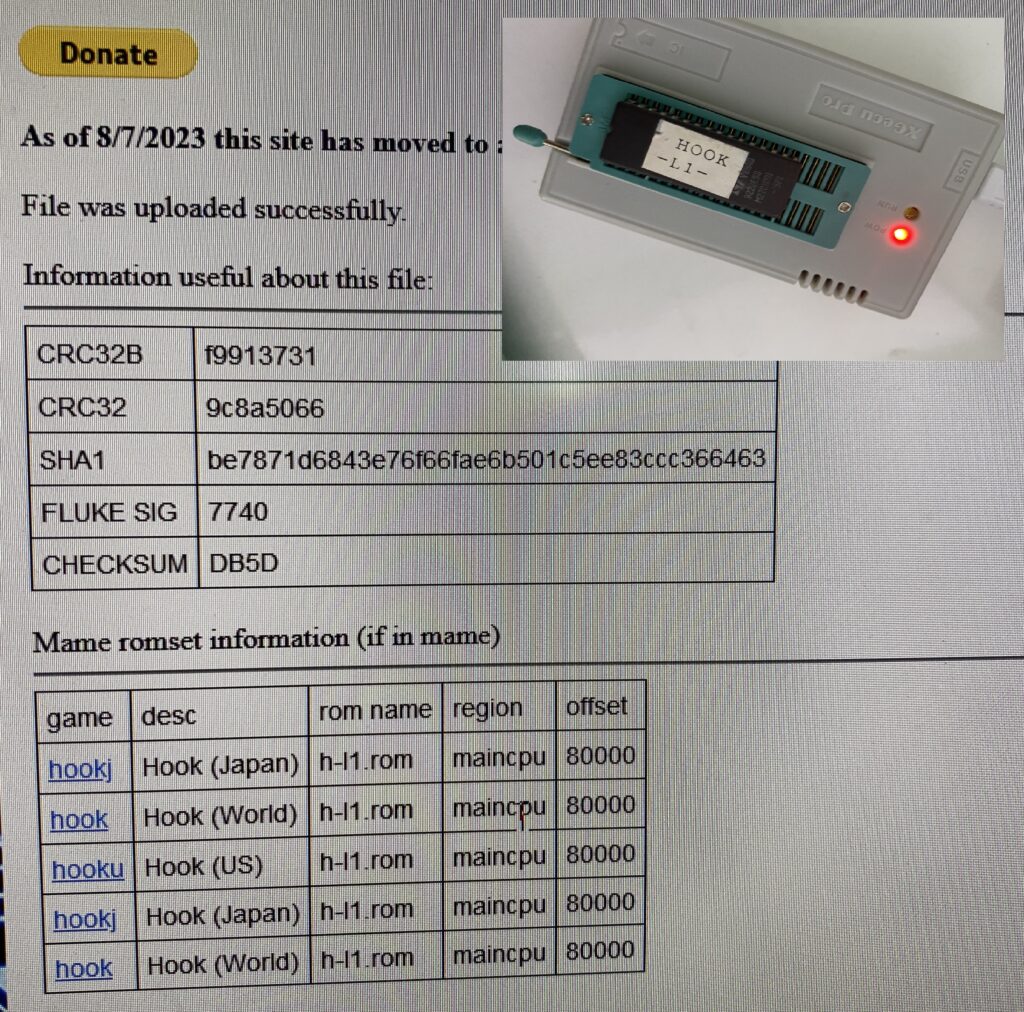
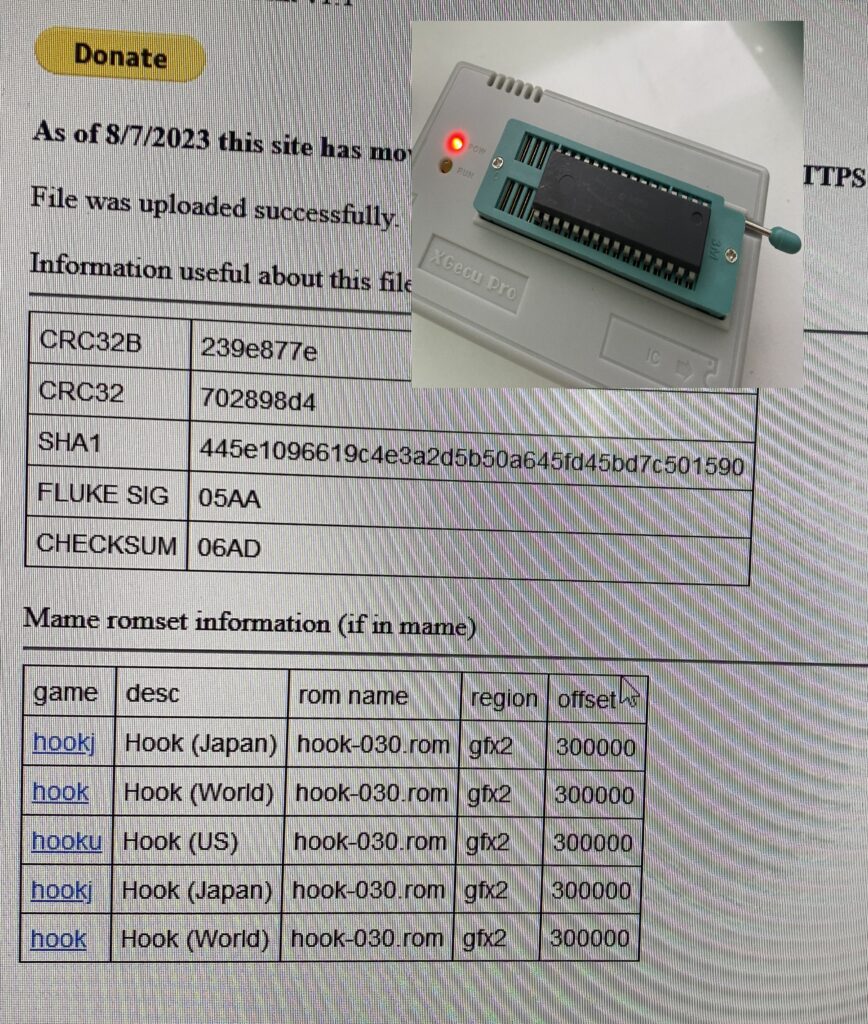

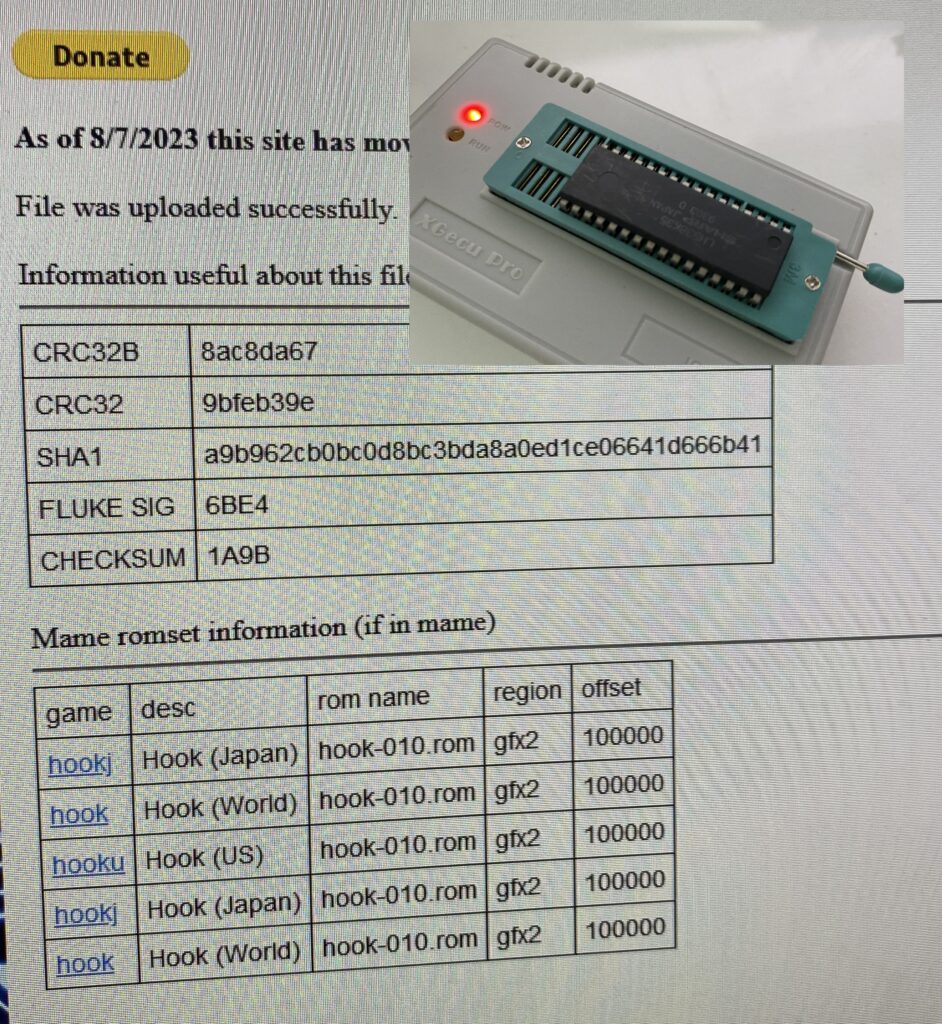
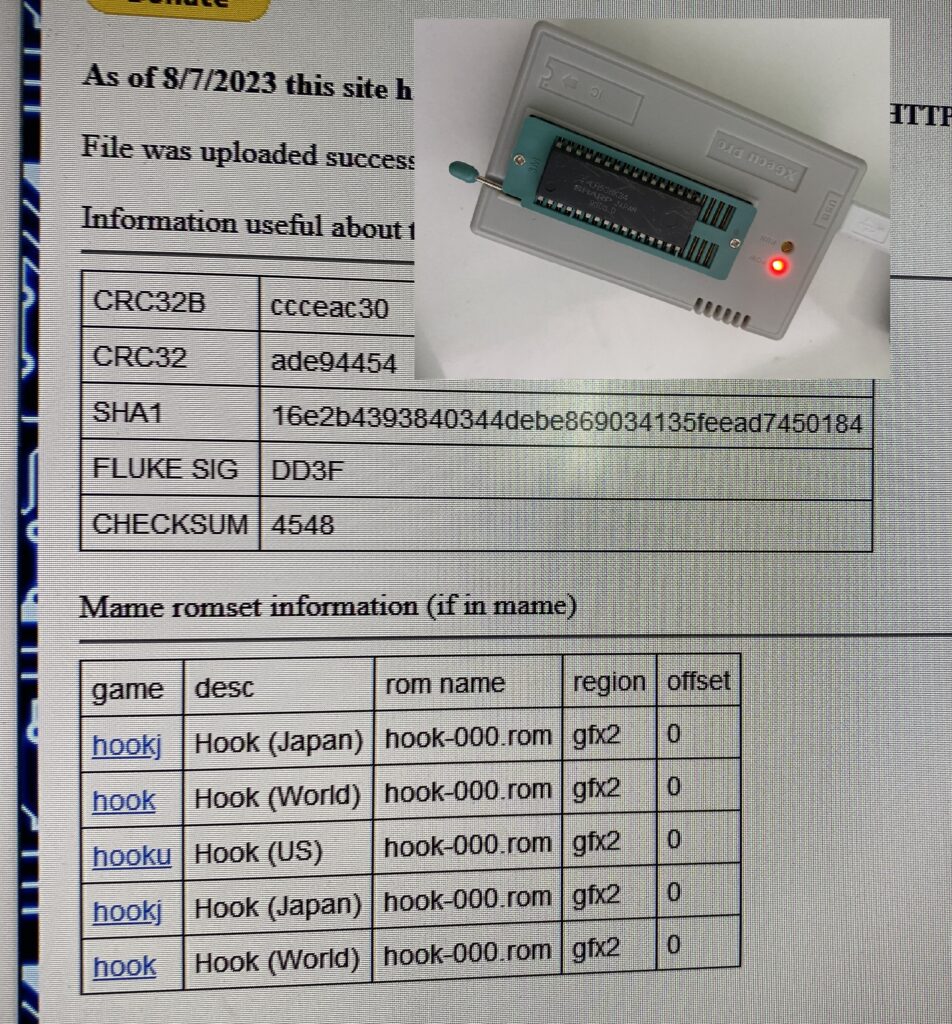
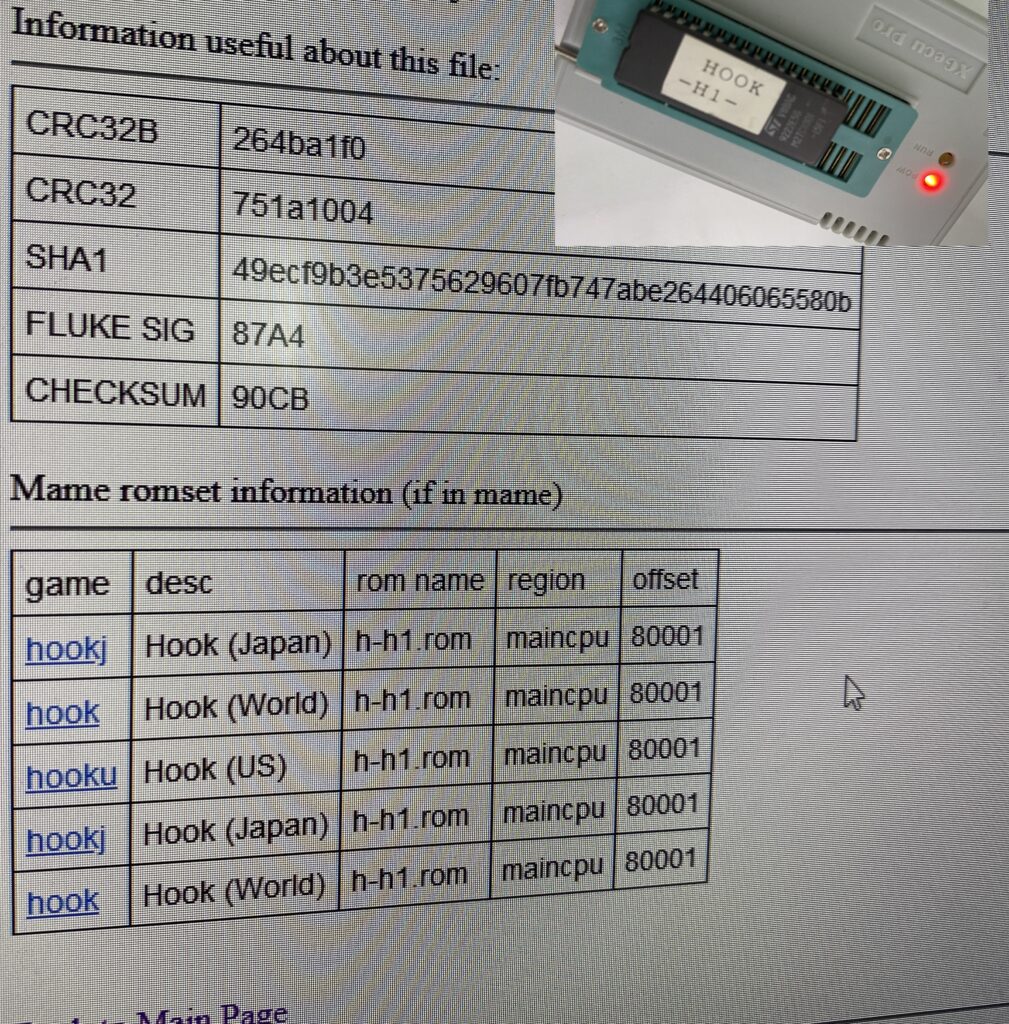
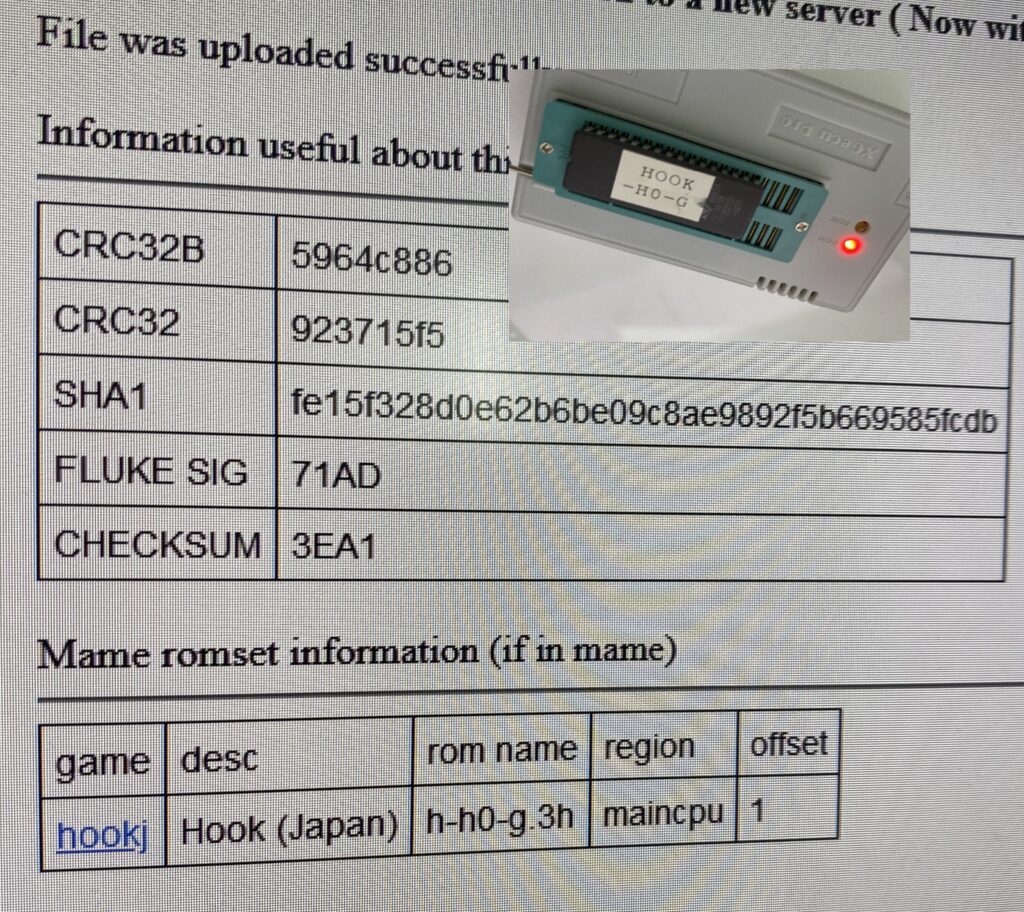
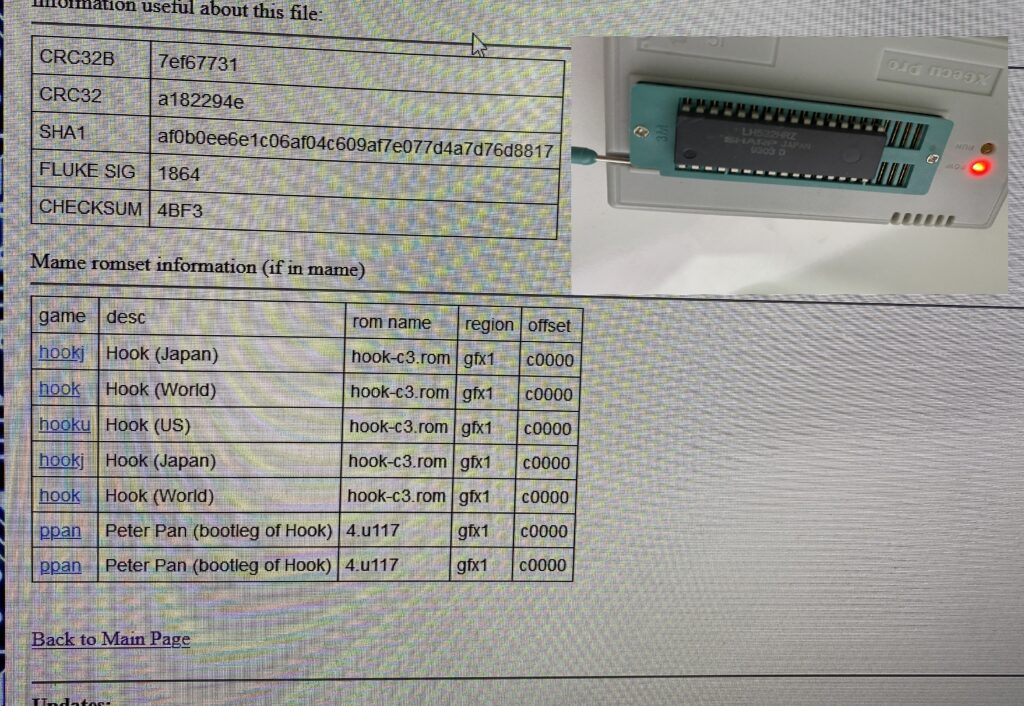
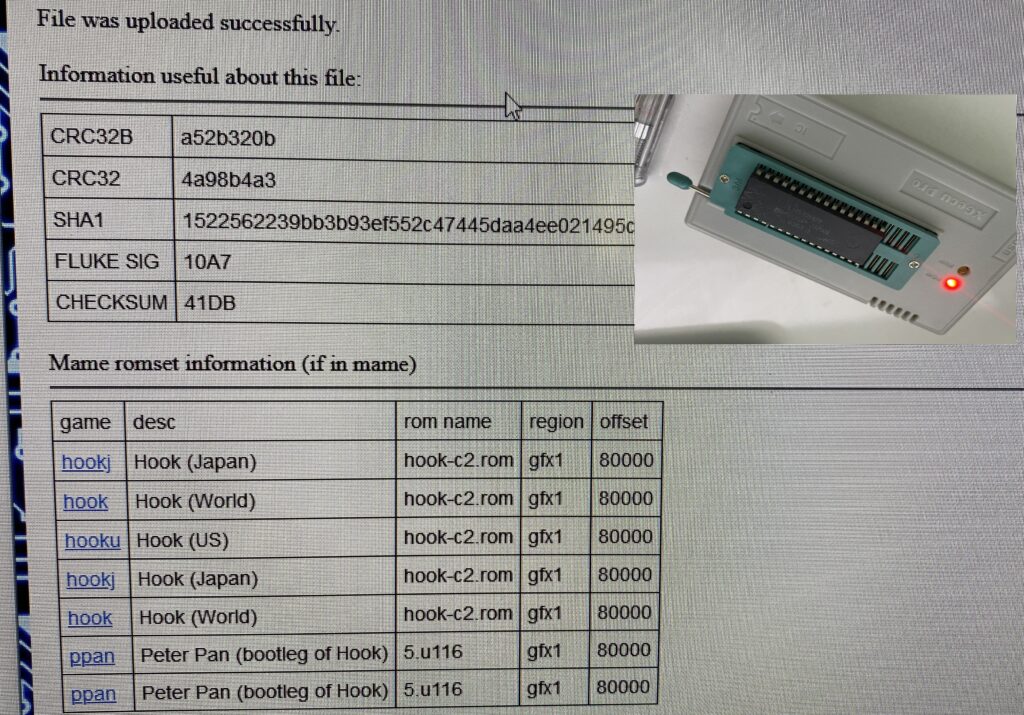
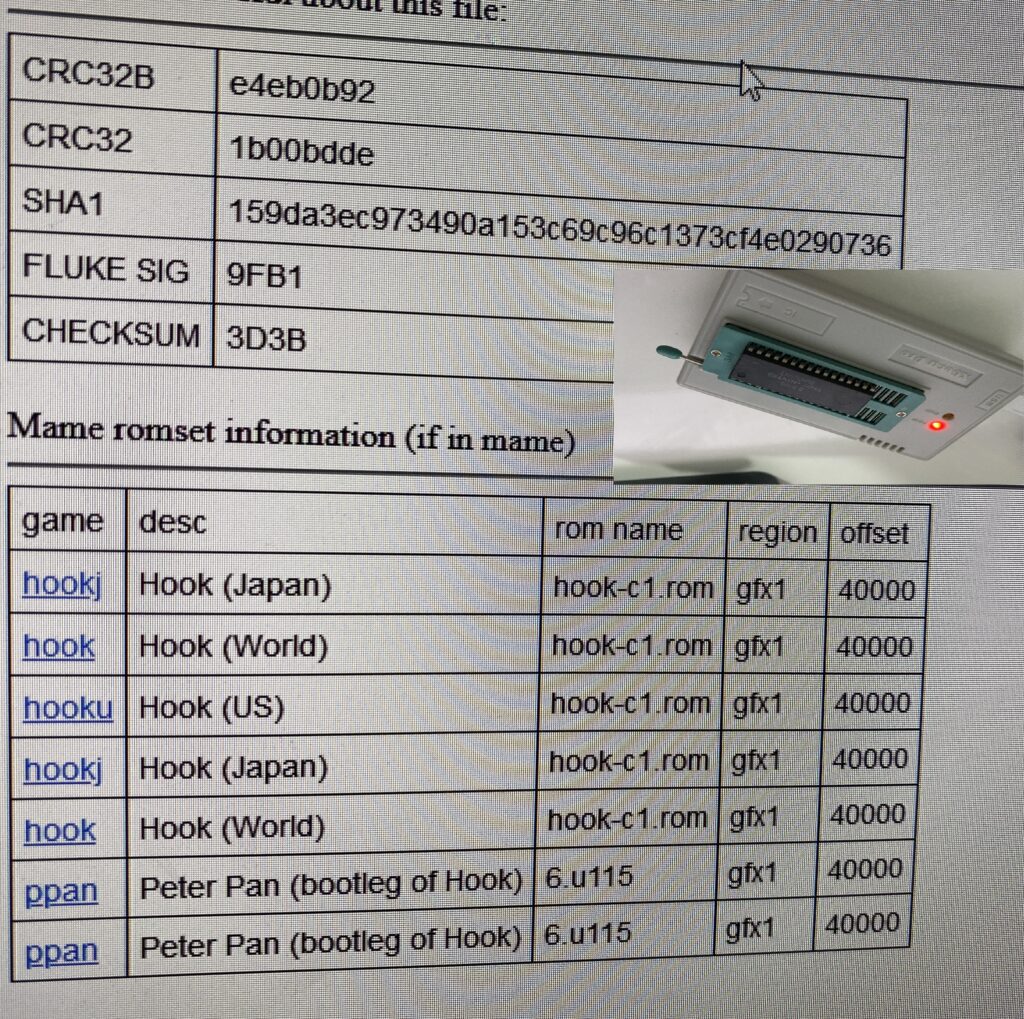
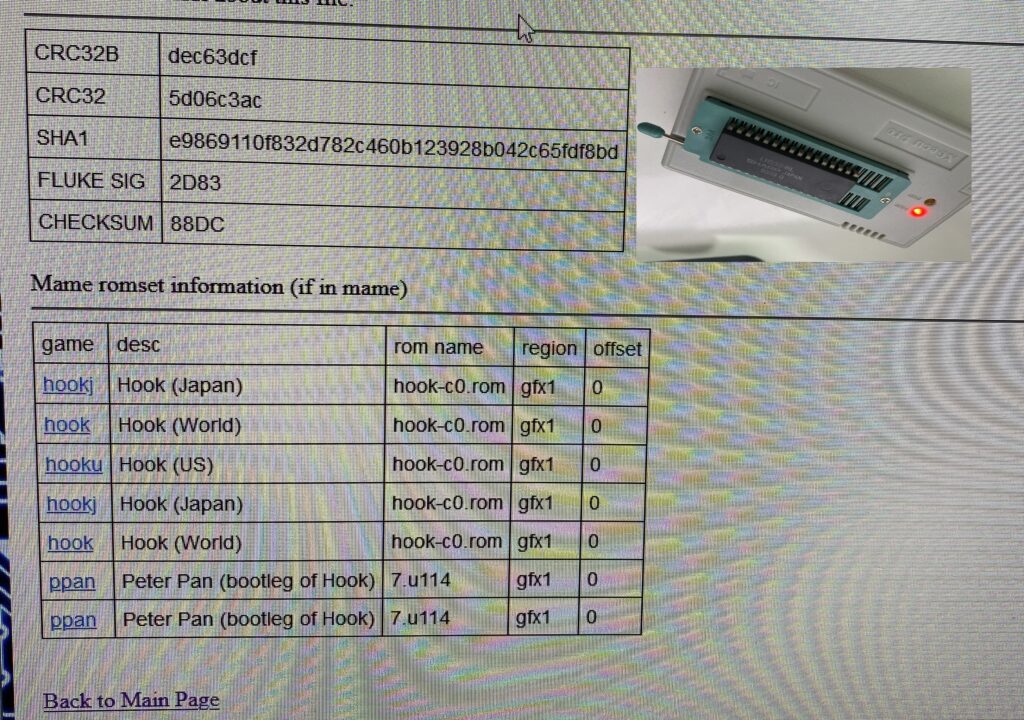
Then I had problems with 2 ROMs – both audio ROMs.
SLO-A and SHO-A
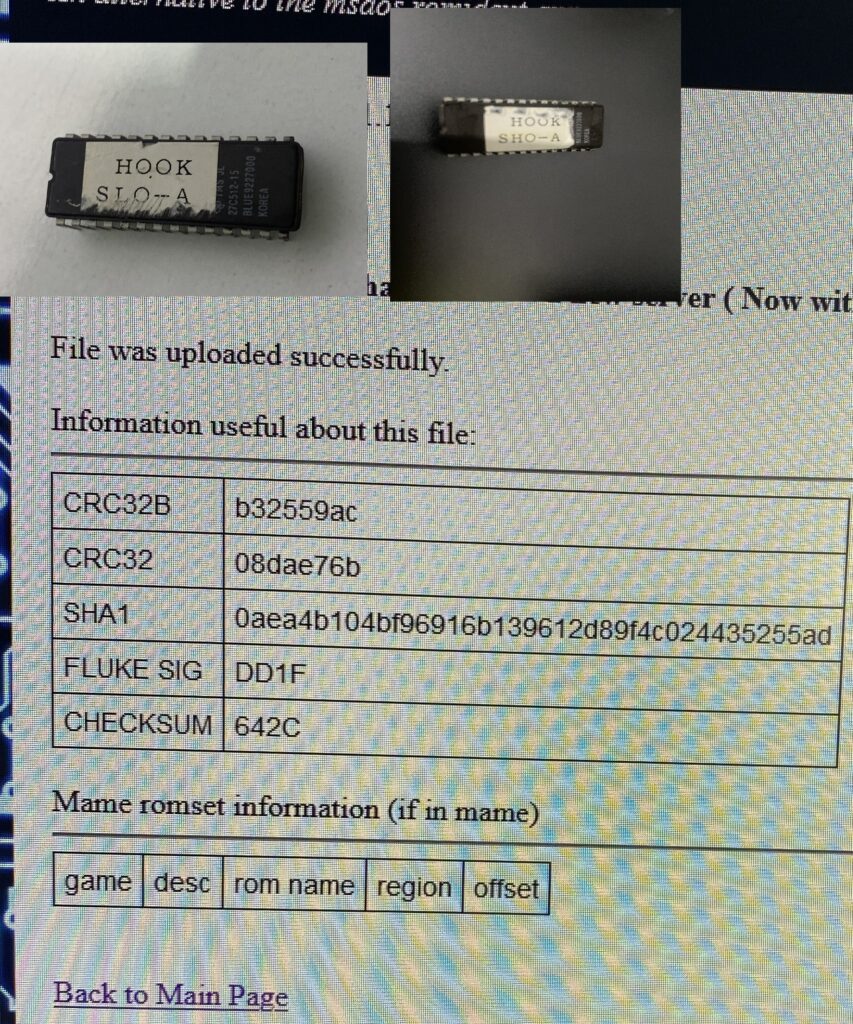
The ROMs are responsible for the playback of all sounds. These ROM comparison sites do not list results if the ROM dump I provide is not 100% identical.
The sound works on this board, so obviously our problems have nothing to do with the audio ROM. I won’t dwell on it, but I’d still like to check how close the files are. Here’s what the “romcmp” command in MAME says about my dumps compared with the correct MAME ROMs:

Next, I am inspecting these two large GA (Gate Array) chips. These are custom chips – when they fail, it is a nightmare to source replacements. Sometimes reproduction parts are created by the community but otherwise you have to source parts from a donor.
GA21 and GA22
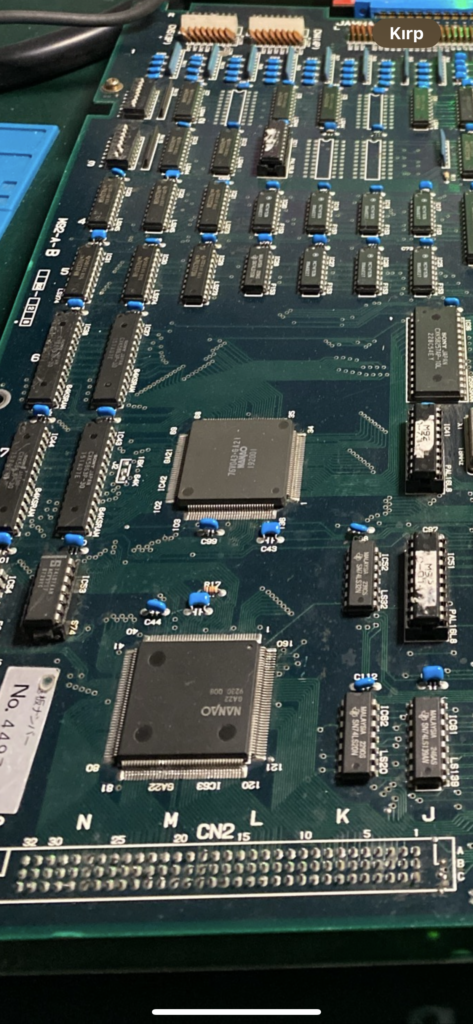
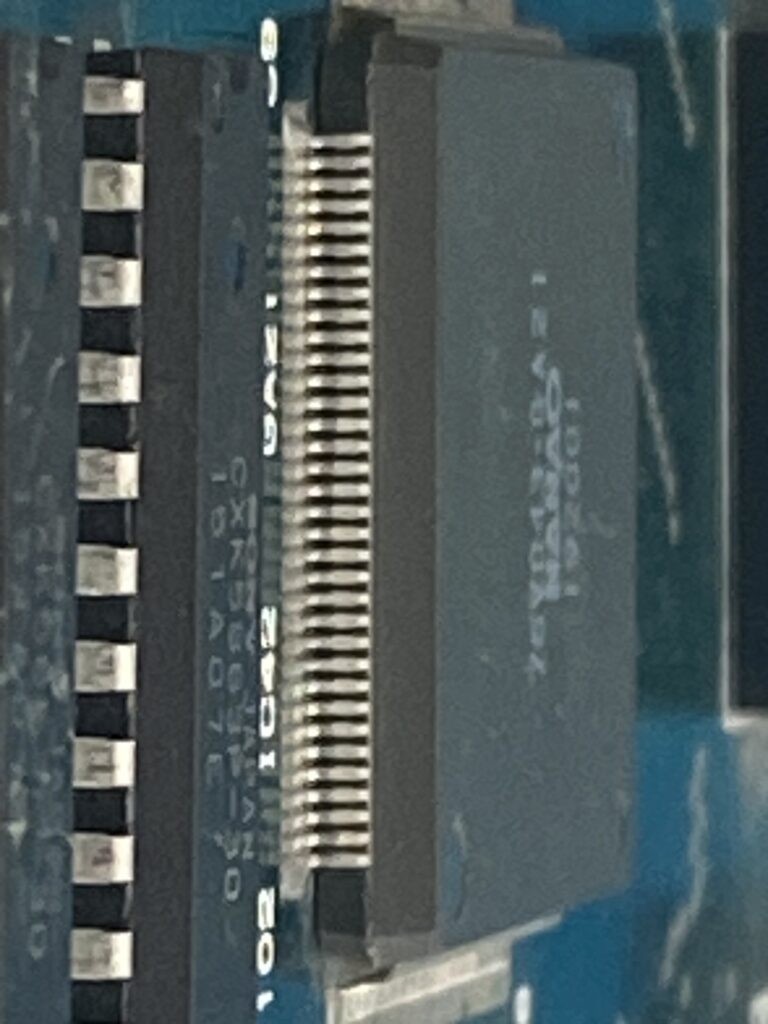
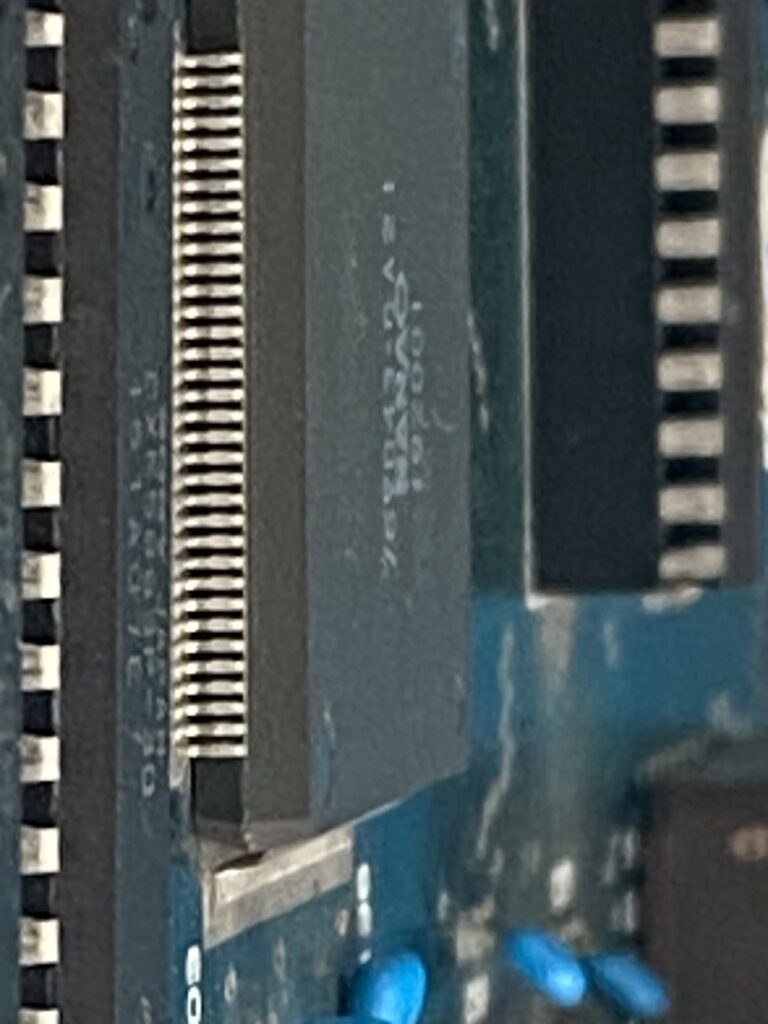
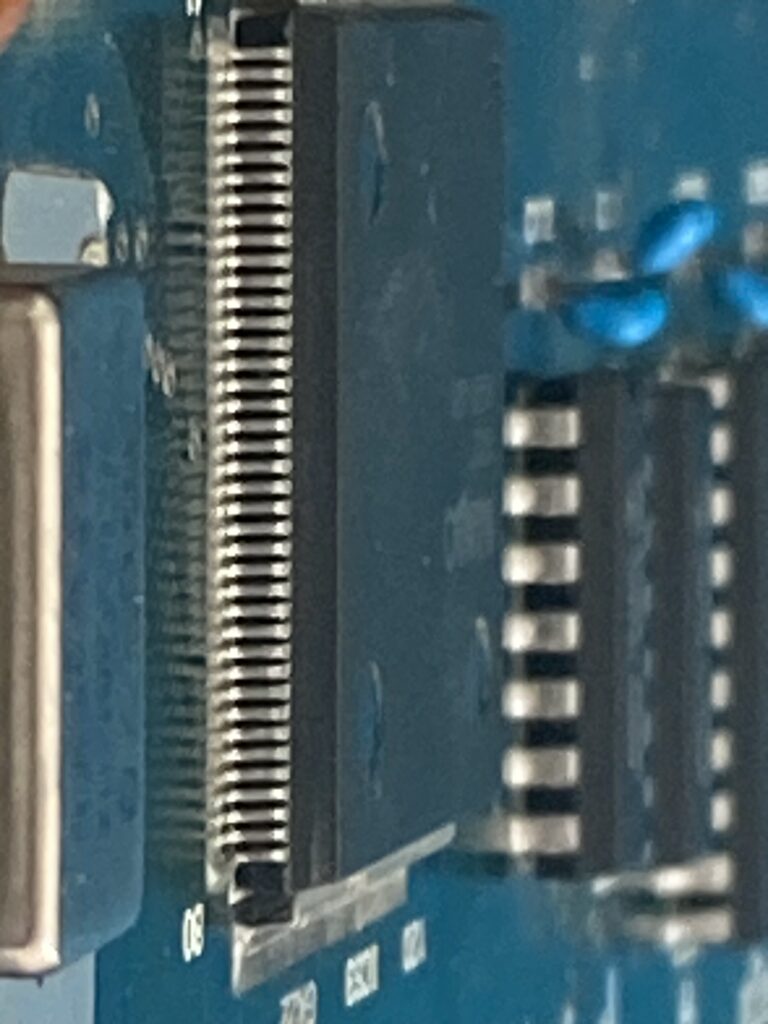
I check the connections of the legs with the boards by gently poking them with an X-Acto knife. I also perform a continuity check with a multimeter to see if there are any bridged paths.
I don’t detect any non-contact legs, but I detect continuity in legs 35 and 36 in GA21.
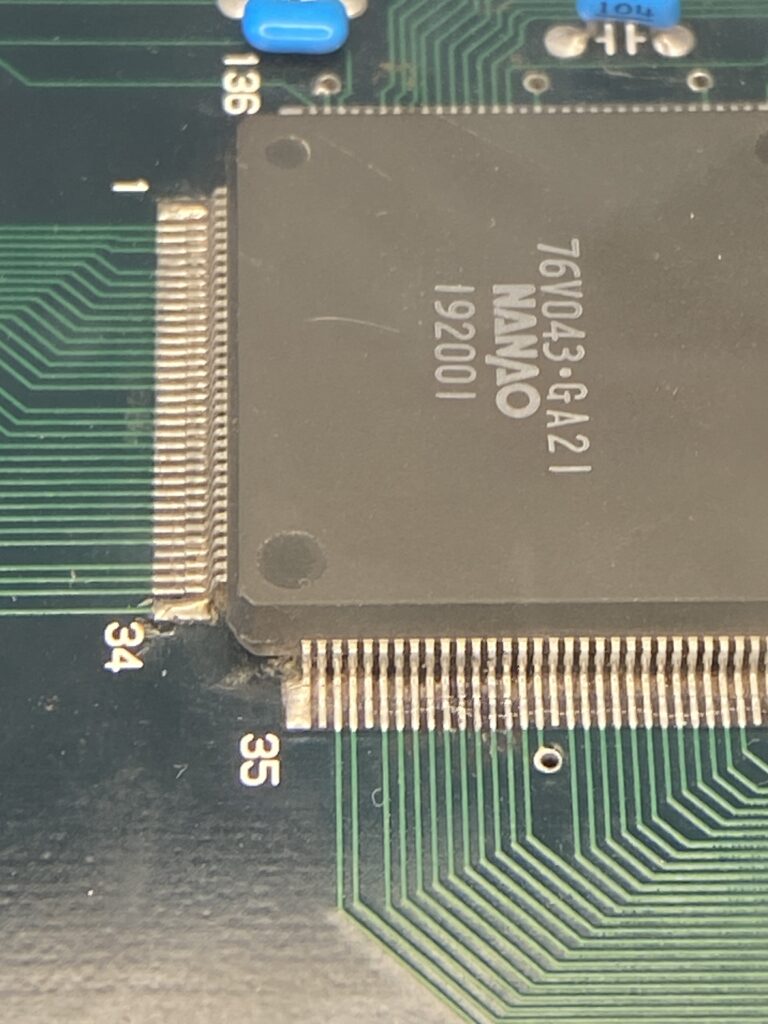
Up close, I don’t see a soldering bridge.
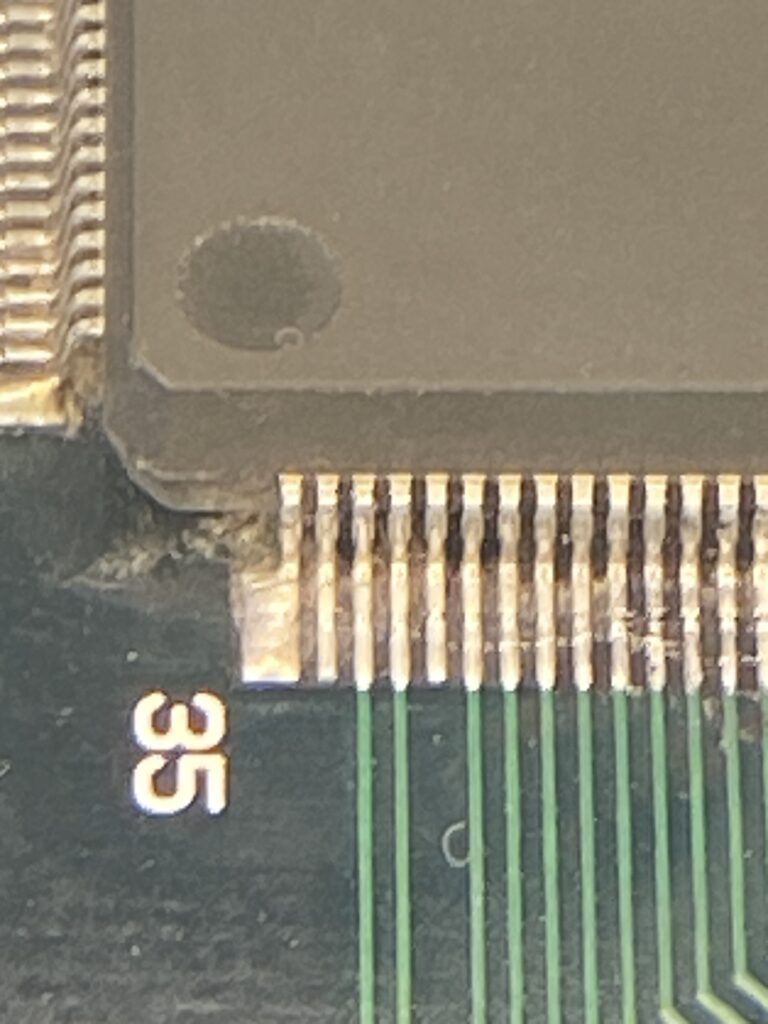
Later on, I asked a friend who has the same board to check on his board, and he gets the same measurement, so there is no problem with these pins. On my board, I reflowed the solder on them just in case.
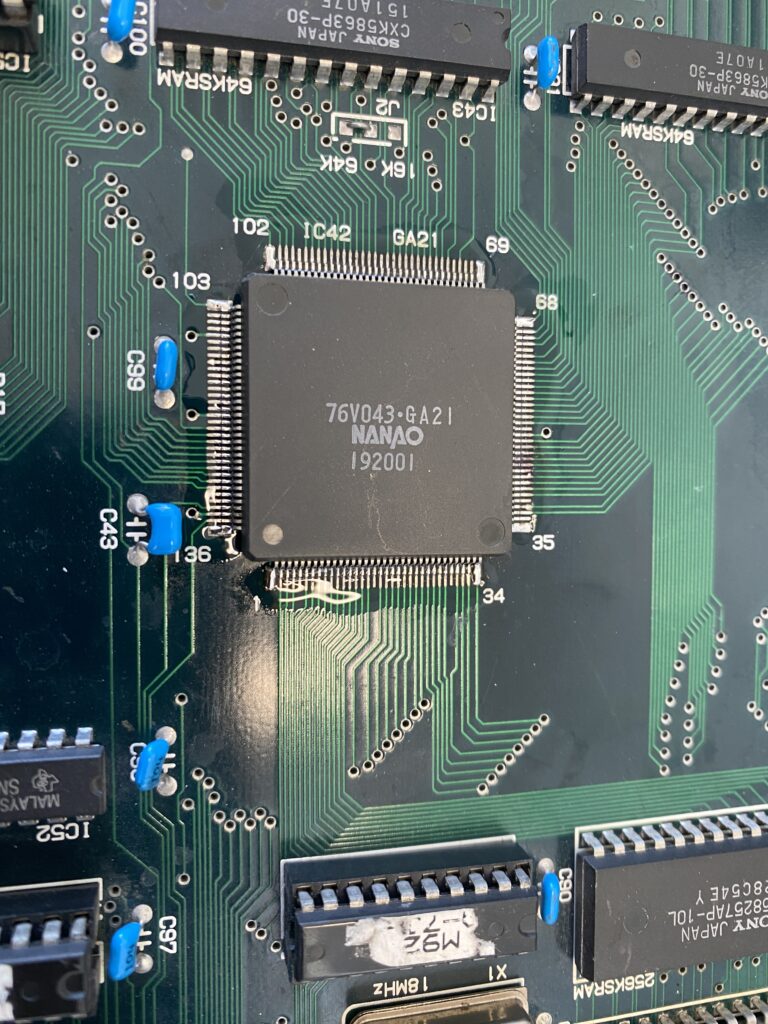
I went ahead and reflowed the other GAs too.
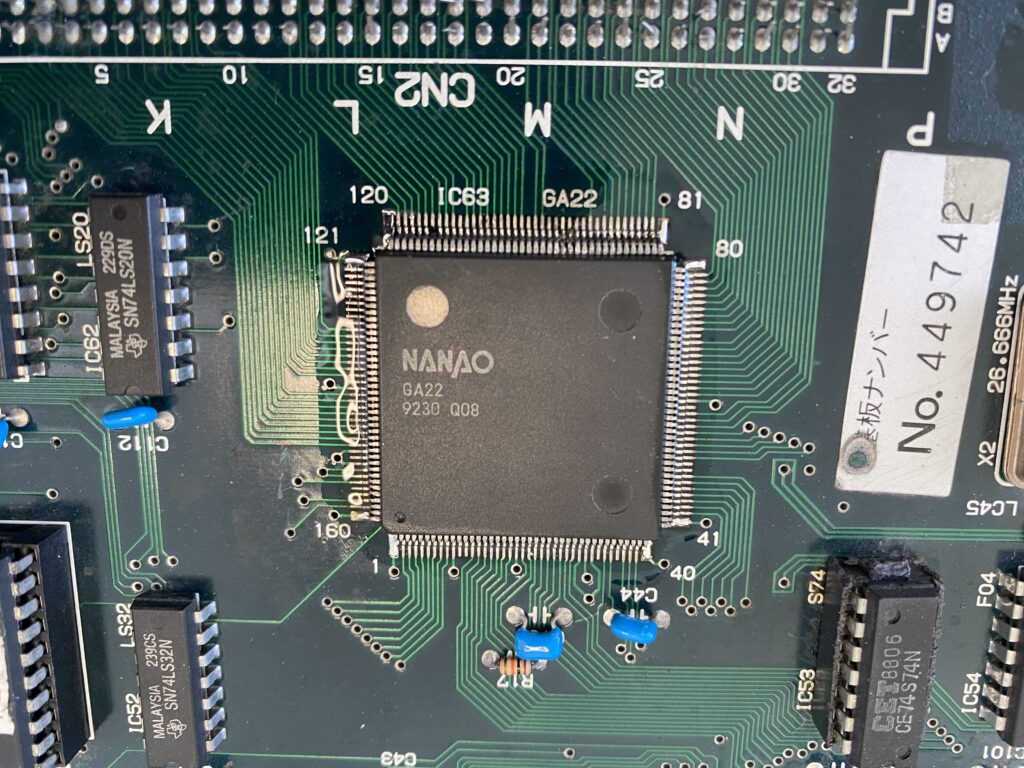
When testing the game again afterwards … the result is the same. I still haven’t found the culprit…
I’m growing weary with this board, but I wanted to get one more thing out of the way. There are 14 brown ELNA capacitors on the motherboard. These capacitors are very prone to leaking so I thought I would replace them.
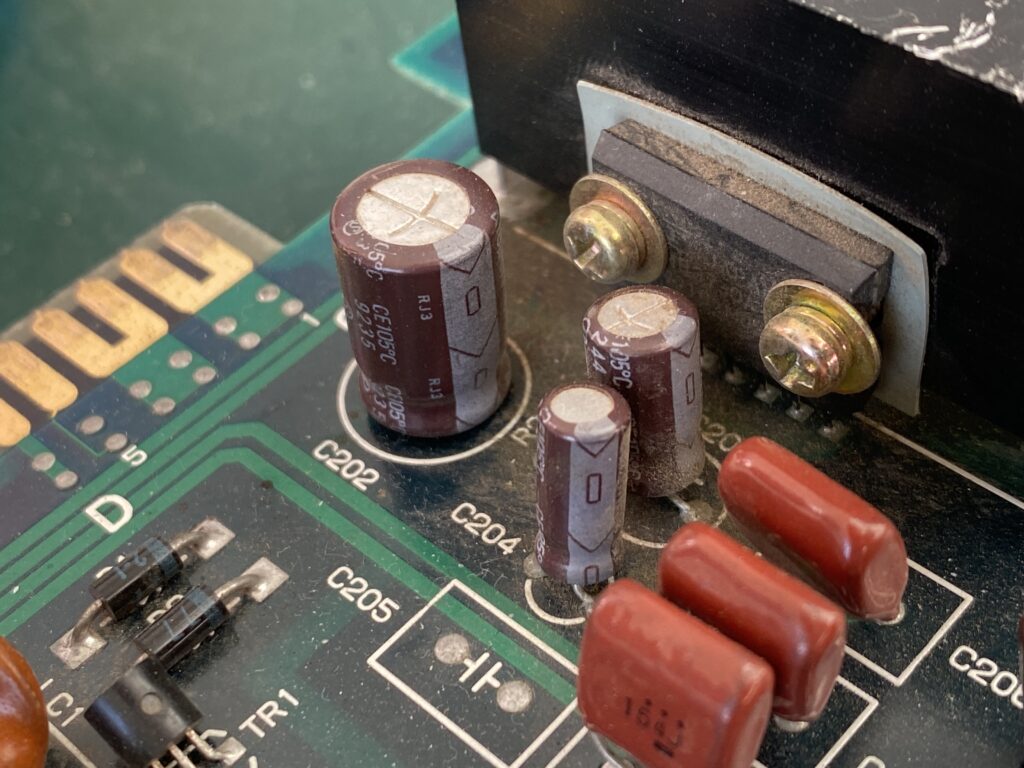
Here is the list:
Irem ‘M92-A-B’ Motherboard Electrolyte Capacitor List
C201 1uF 50V
C202 470 uF 25V
C203 220uF 10V
C204 22uF 25V
C209 100uF 25V
C210 1uF 50V
C213 47uF 16V
C215 1uF 50V
C216 1uF 50V
C217 1uF 50V
C218 1uF 50V
C219 1uF 50V
C236 100uF 25V
Here’s all of the old capacitors removed:
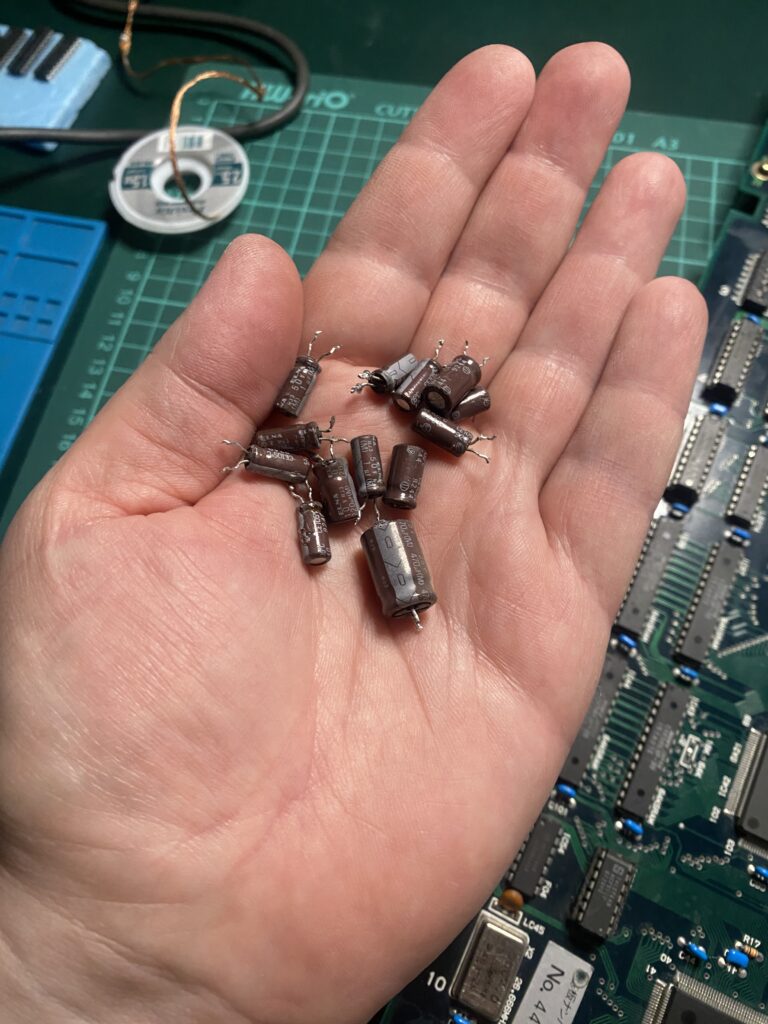
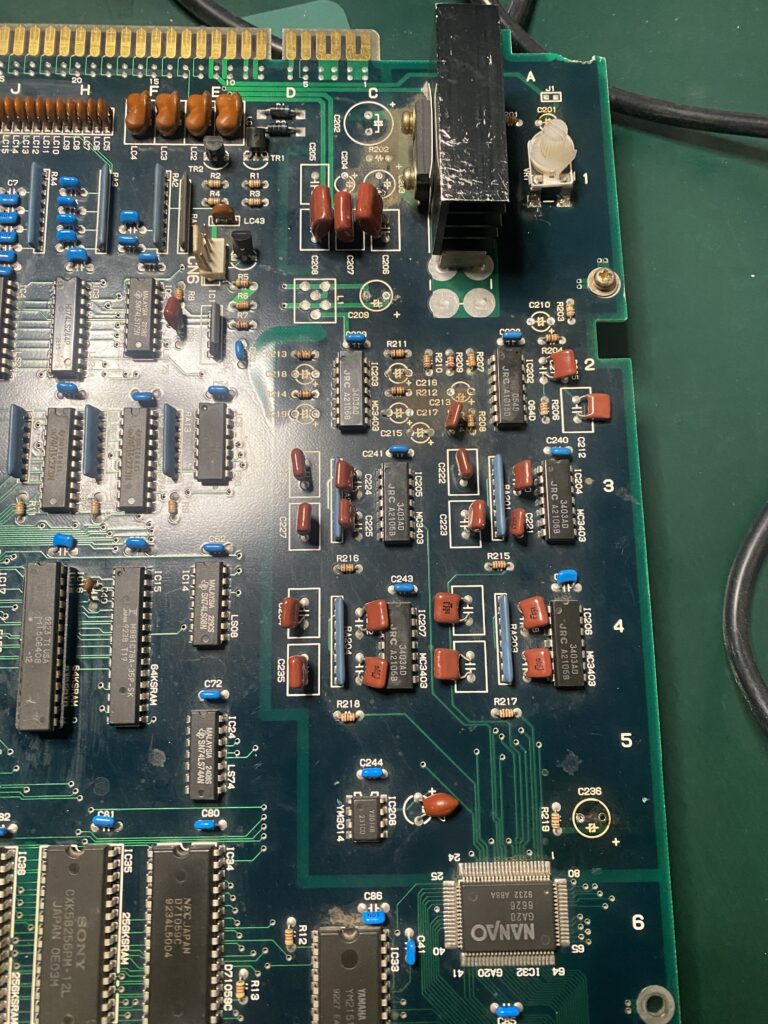
And here’s the board after installing the replacement caps.
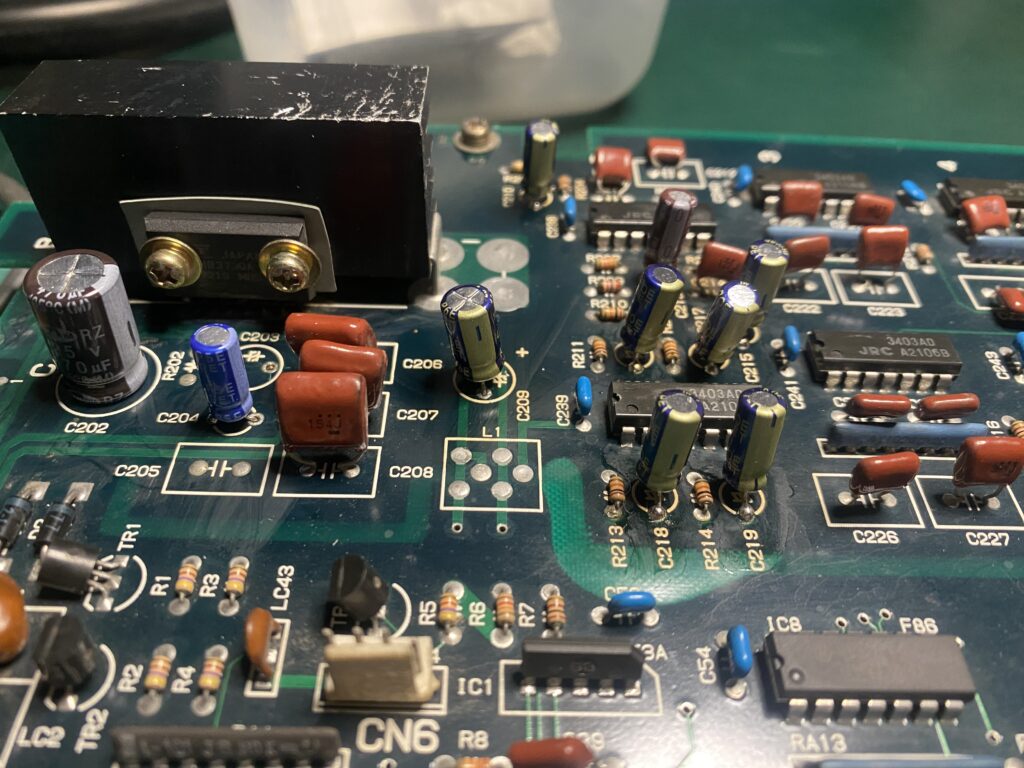
If you’re using a hot air gun, be VERY, VERY careful! This area highlighted in blue swelled on my board-fortunately I didn’t damage anything. I dodged a bullet.
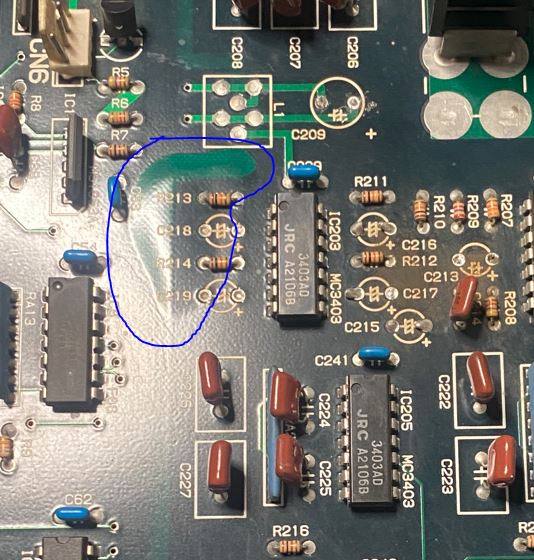
After recapping, the previously almost inaudible game sound now sounds great!
Now back to the main problem with the horizontal lines at the bottom of the screen, the vertical lines on the right and left of the screen, and the color distortions when the background scrolls.
I take out my Logic Probe and start probing. There are two palette RAM chips located at IC15 and IC16 on the motherboard. These parts are Fuji brand – the most susceptible brand prone to fault. The part is MB81C78A, which is 8K x 8 = 64KB of RAM.
I documented the logic activity of the pins on the two chips by making a table:
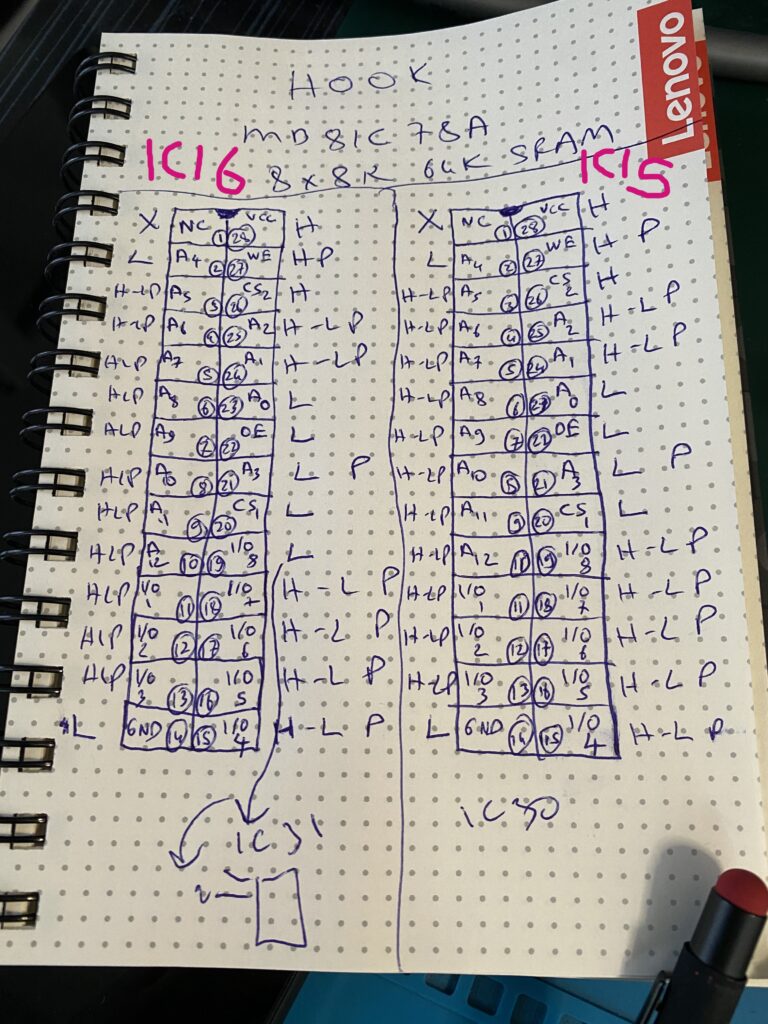
According to the data sheet for these memory parts, Pin 19 on these parts is the “I/O 8” data line. When probing this pin, I see a difference between IC15 and IC16.
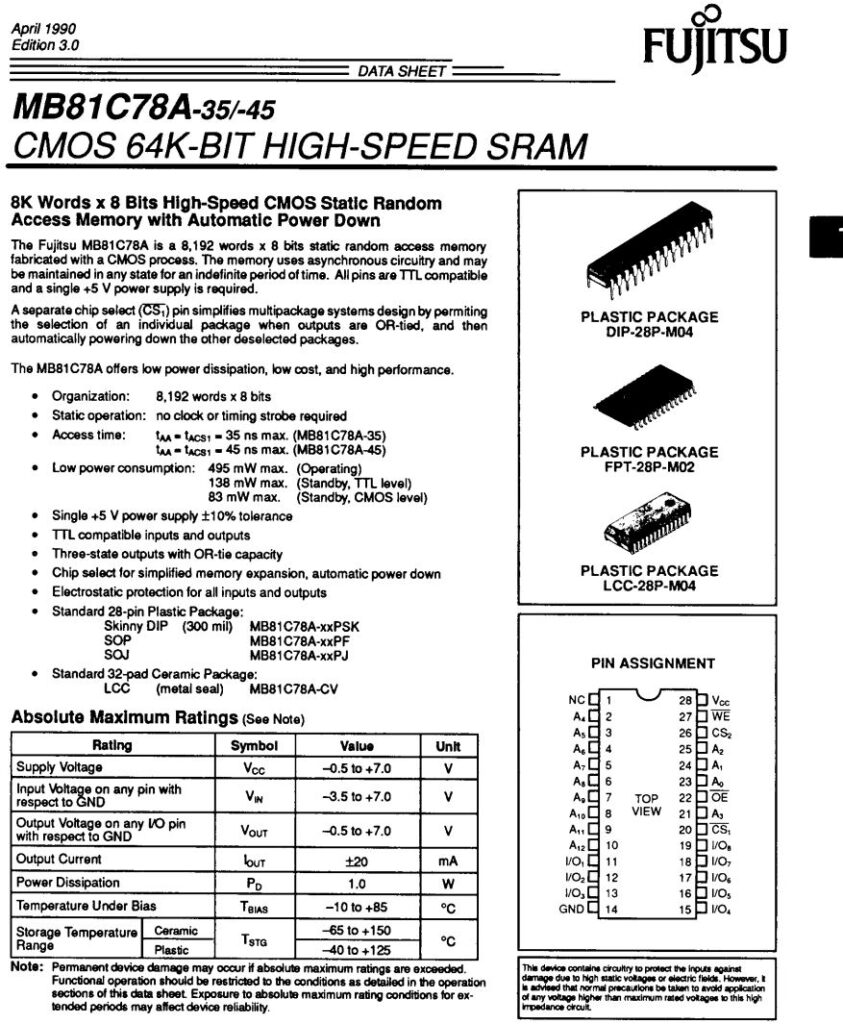
IC 15 –> Pin 19 –> shows PULSE activity between HI and LOW. So there is a data flow.
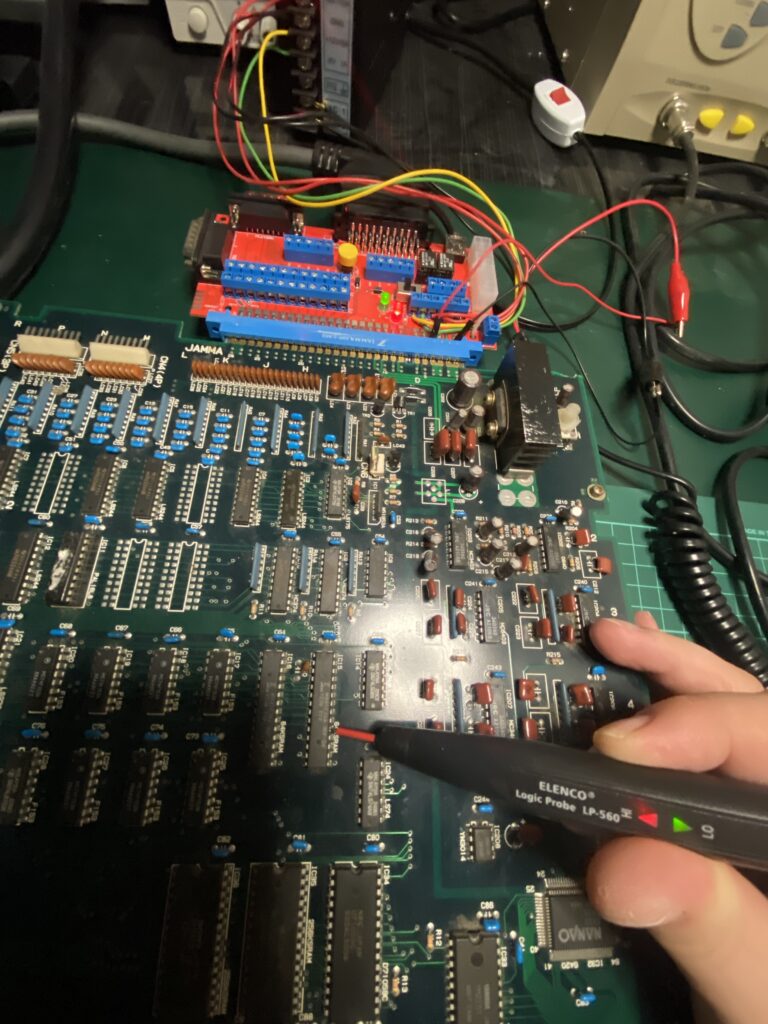
IC 16 –> Pin 19 –> LOW only and no PULSE. So no data is flowing.
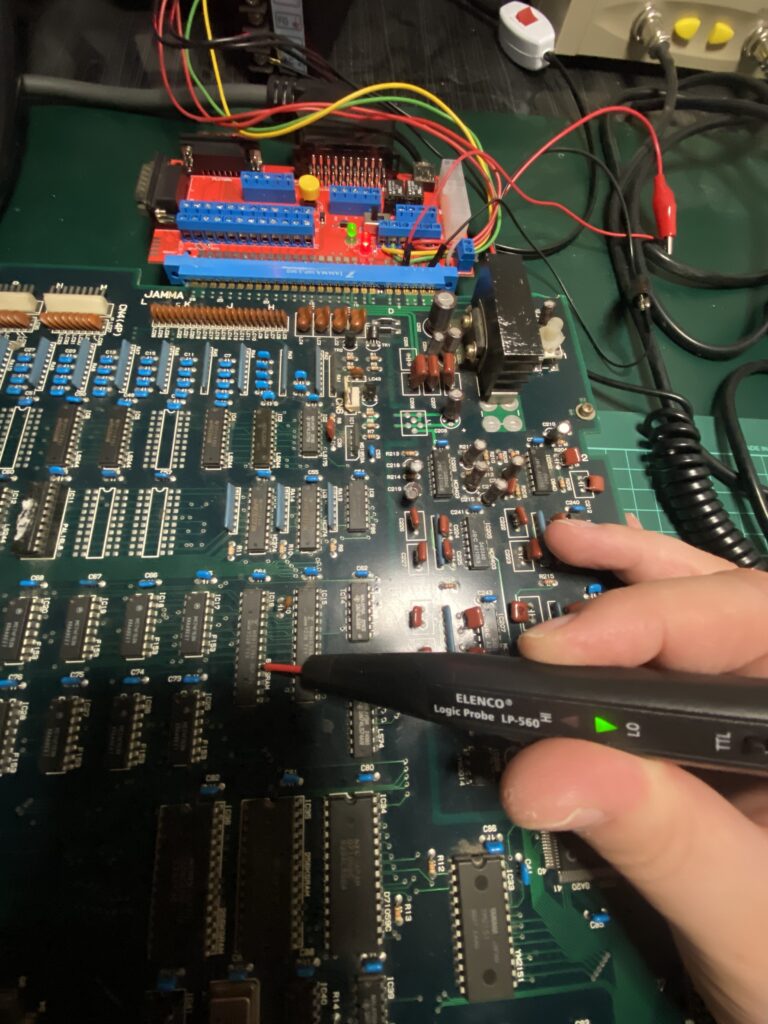
Two things could be happening here:
1) This RAM chip is bad
2) Or one or more ICs connected to this pin are bad.
I trace Pin 16 of IC19 with a multimeter and see that it goes to Pin 31 of IC2.

IC2 is a SN74LS374N part. According to it’s data sheet, Pin 2 –> 1Q (Output)
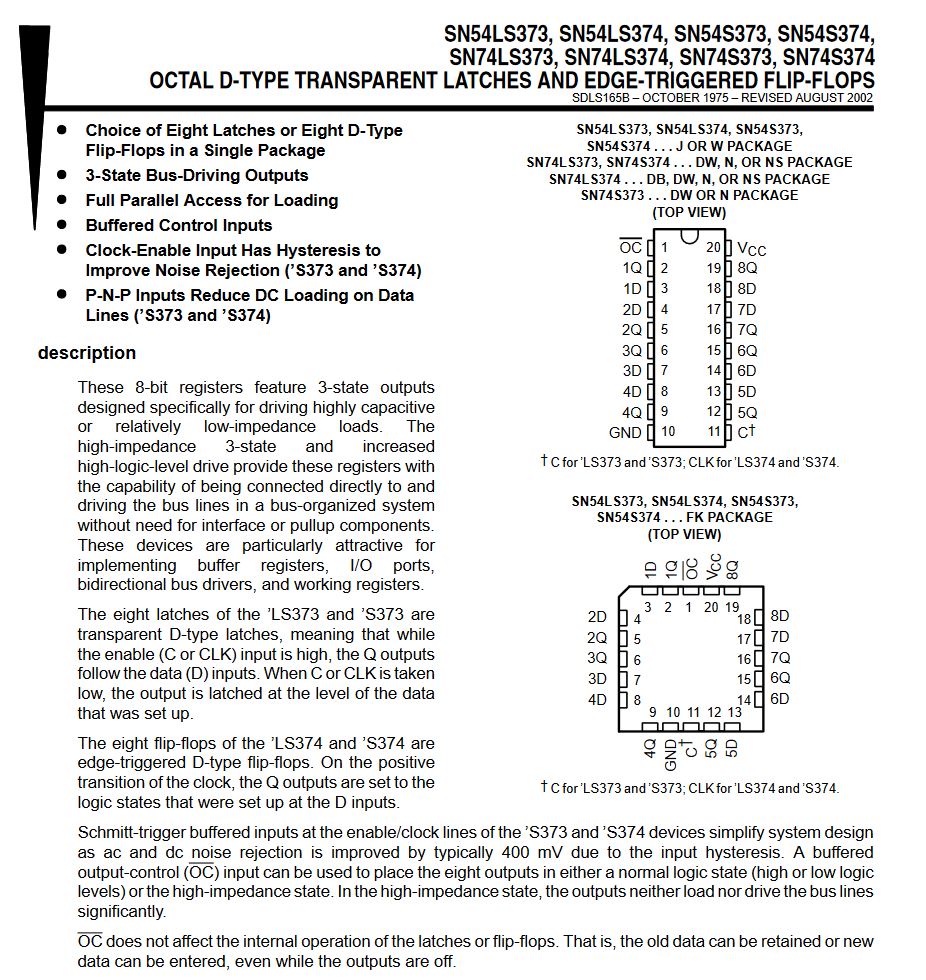
I also find that IC31 Pin 2 also connects to Pin 2 of IC23.
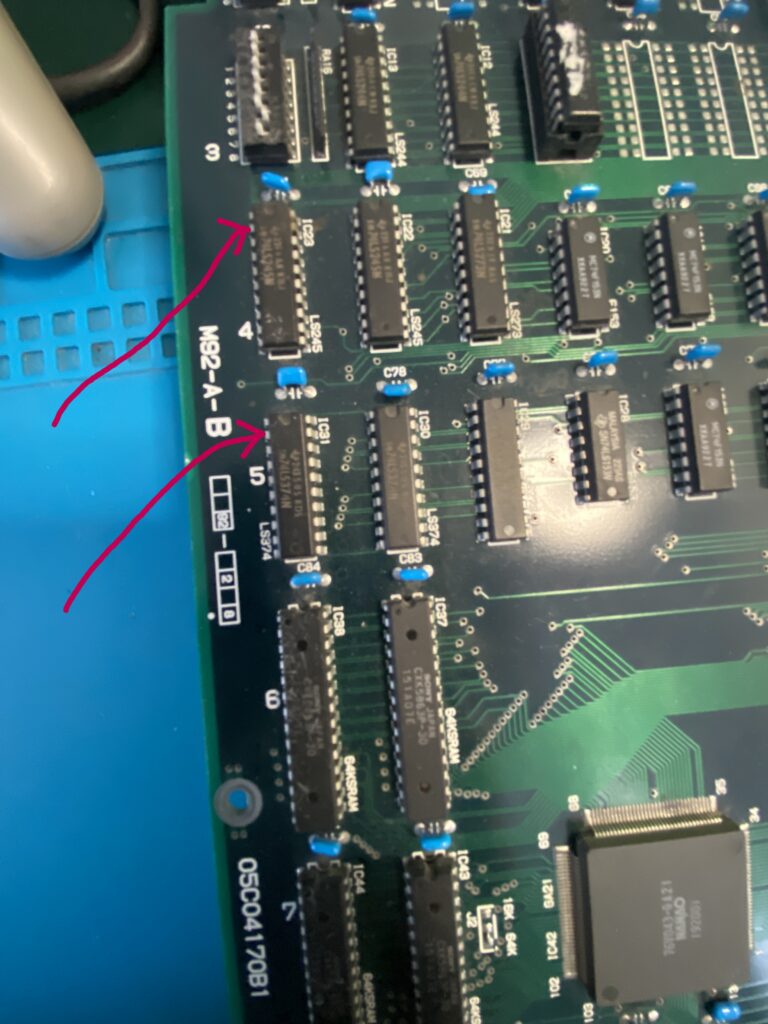
IC23 is a SN74LS245N part. According to its data sheet, Pin 2 –> A1 (I/O)
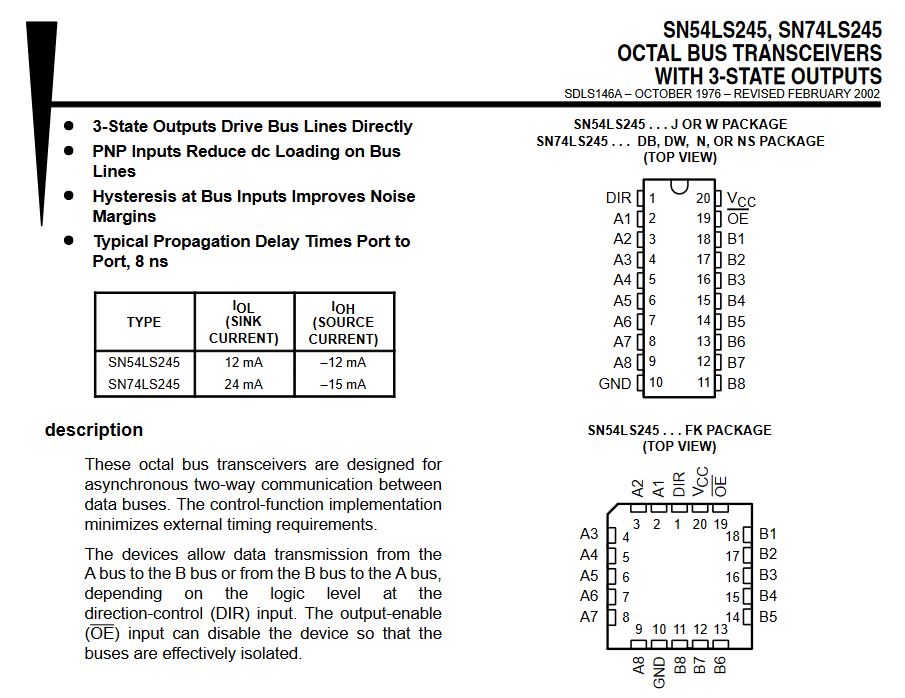
I remove these parts with the suspicion that they are causing at least part of the problems.
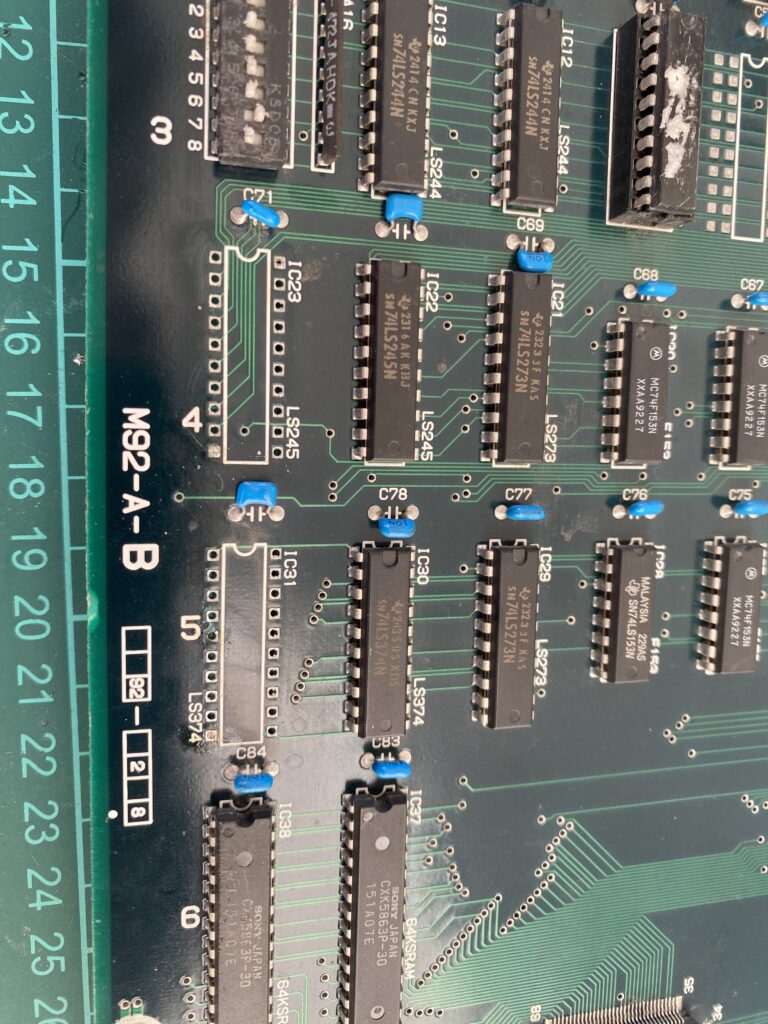
Testing the parts out of circuit in my EPROM programmer, the SN74LS374N chip passes the test.
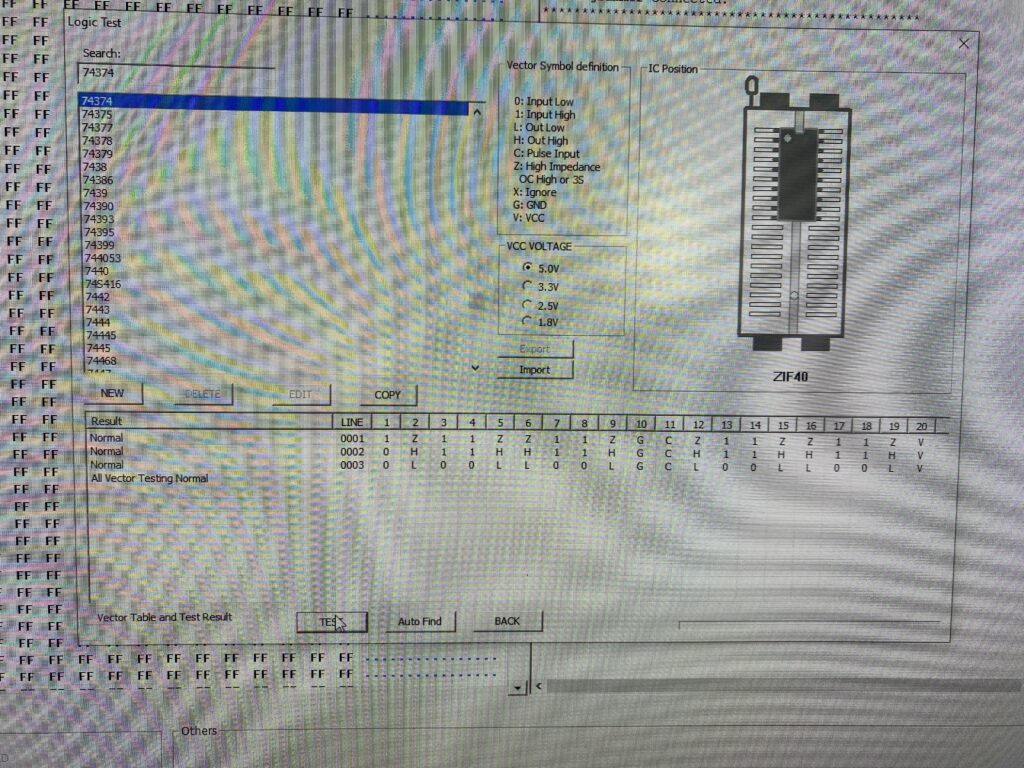
The SN74LS245N part also passes the test.
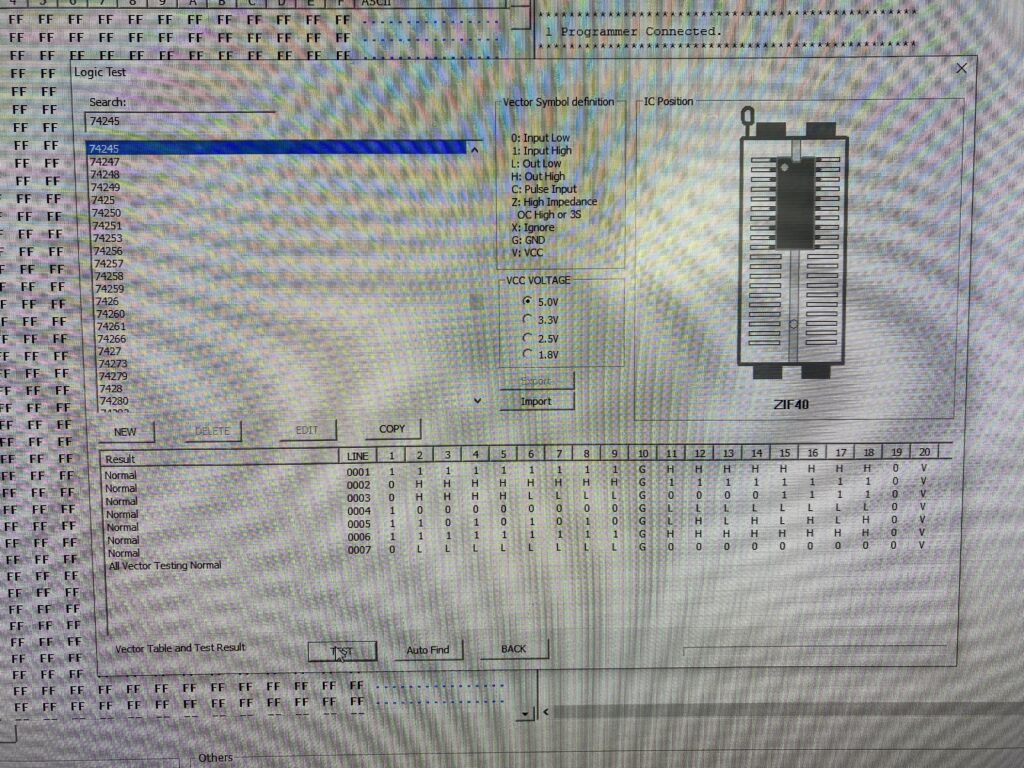
Nevertheless, I install sockets and change them out anyway.
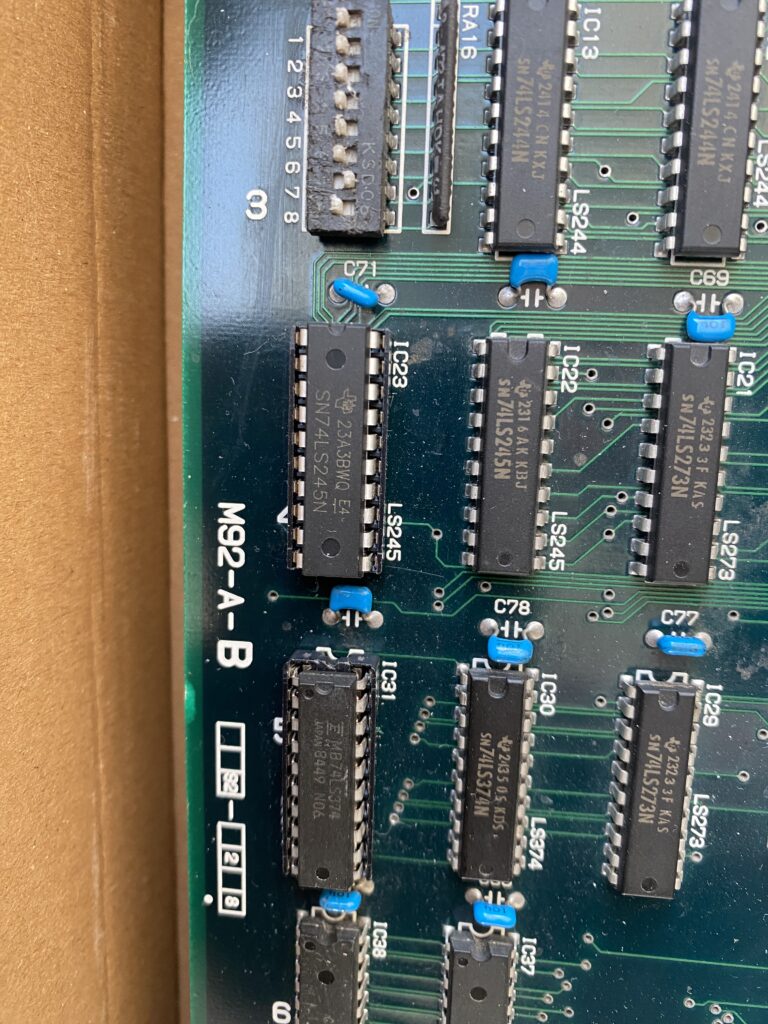
Testing the game afterwards, the result is the same.
Next, I decide to replace the Fujitsu Palette RAM parts as well. I have the following equivalent RAM parts available:
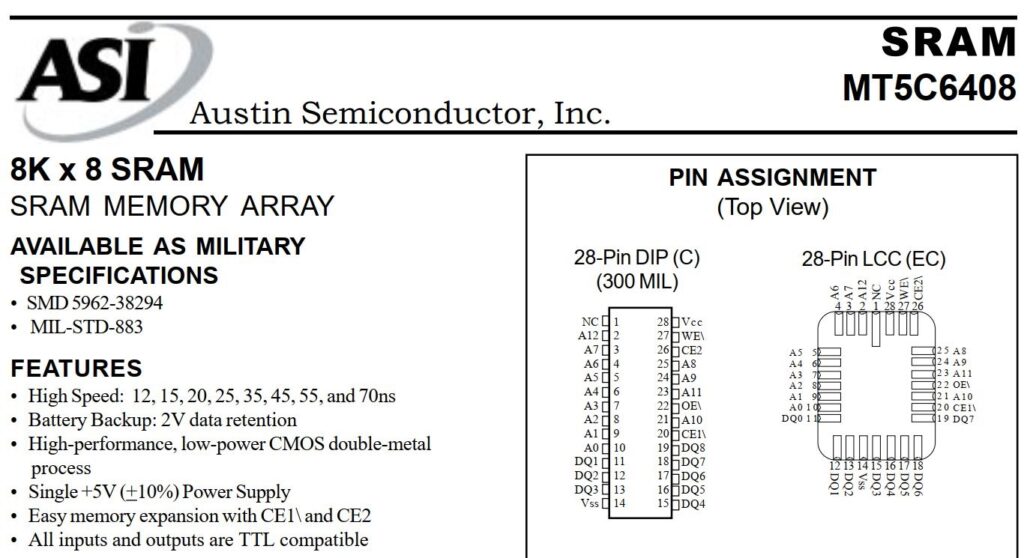
I remove the old RAM and install sockets.
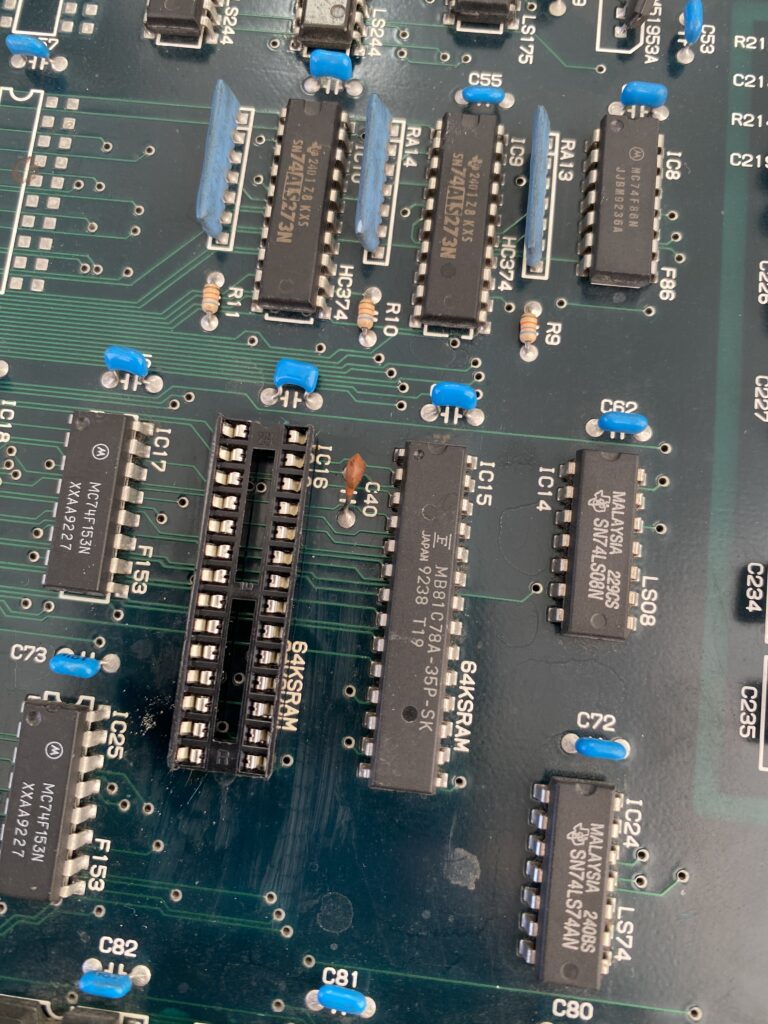
Now, when testing the old RAM out of circuit … they test as faulty.
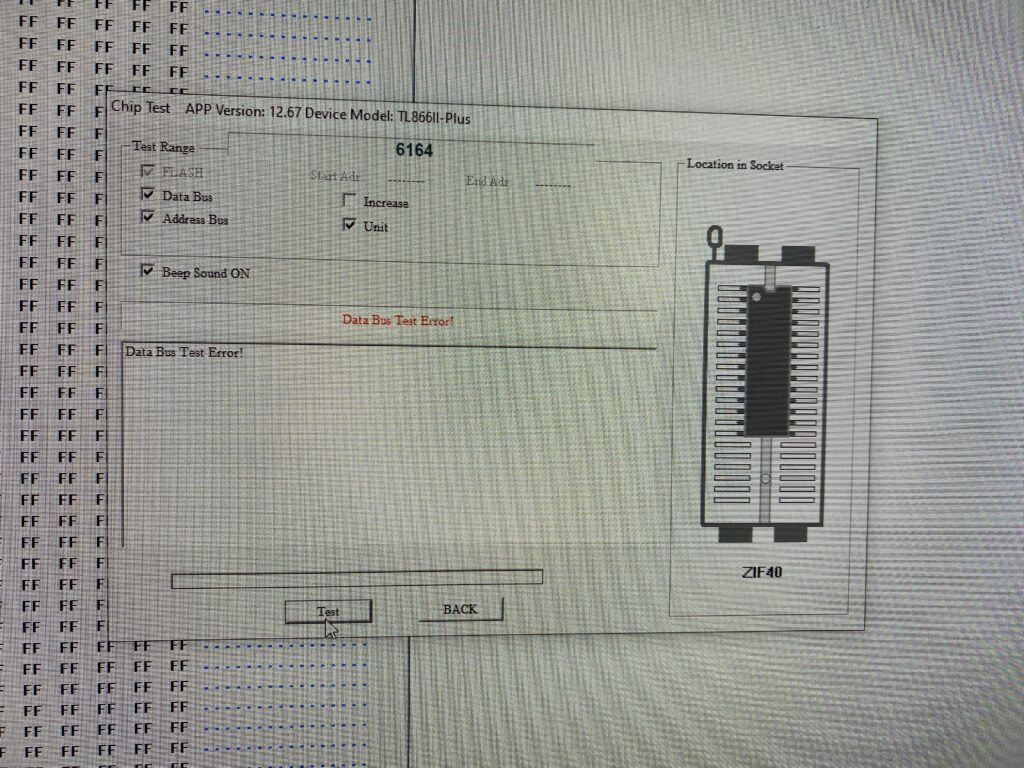
I install a new RAM part that passes the out of circuit test in the socket to replace this faulty part, while leaving the other old Fujitsu part installed in the other Palette RAM socket.
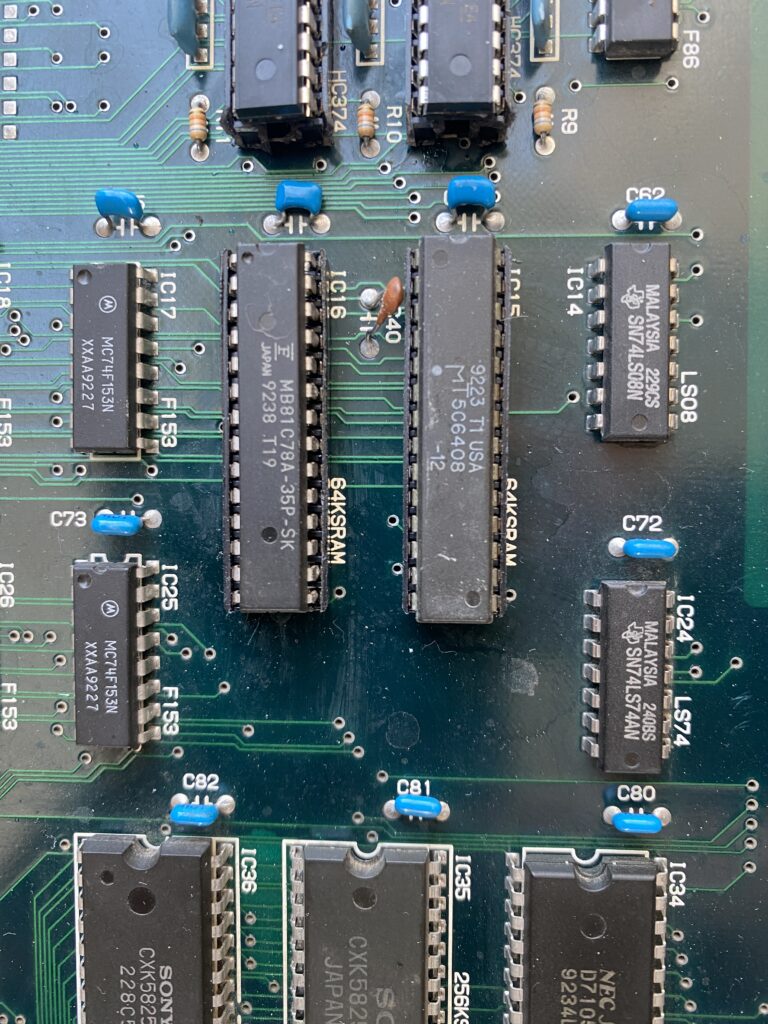
Now when testing the board … everything is worse. Now, in addition to the old problems, there is now a problem with the color Red. As you can see in this video, all of the colors appear in the narrow columns on the left and right, but there is no Red on the main screen in the middle.
I decide to put the board into TEST mode to test the red color. For this, press 1P A+B on the RAM ROM TEST screen. Then, on the menu, select Screen test.
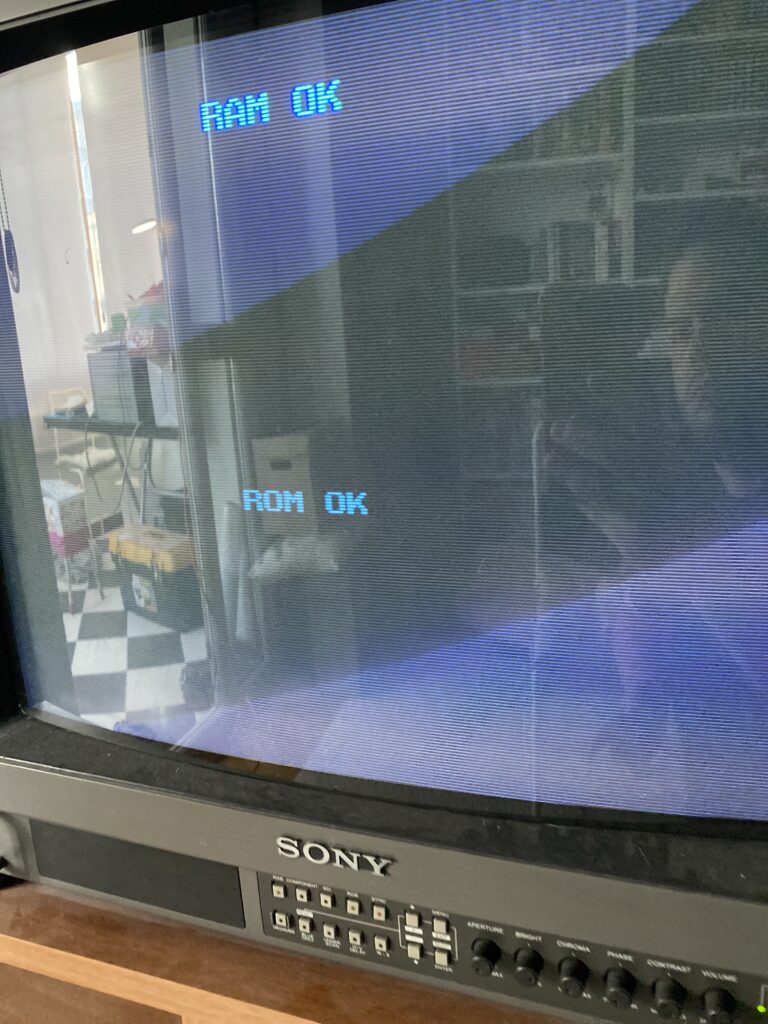
As you can see in the Screen Test, there is no trace of Red.
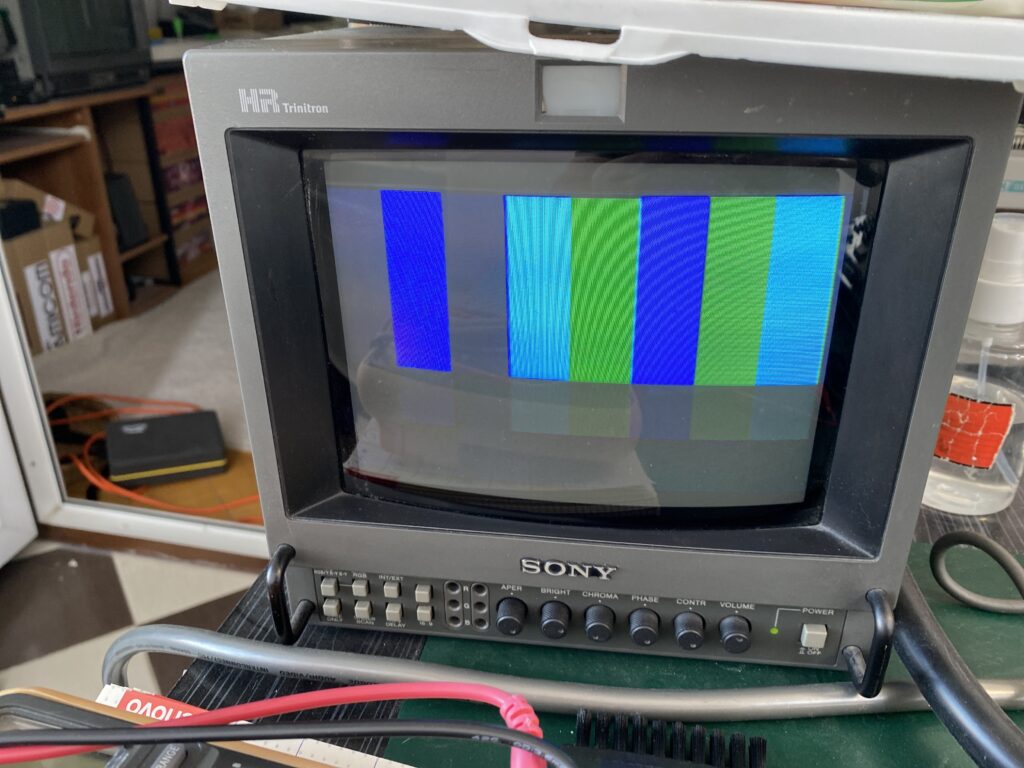
In case I missed something, I check around further with the Logic Probe, and I find another IC on the same line.
Pin 18 of IC10 is connected to the same pin as the others – I missed it before.
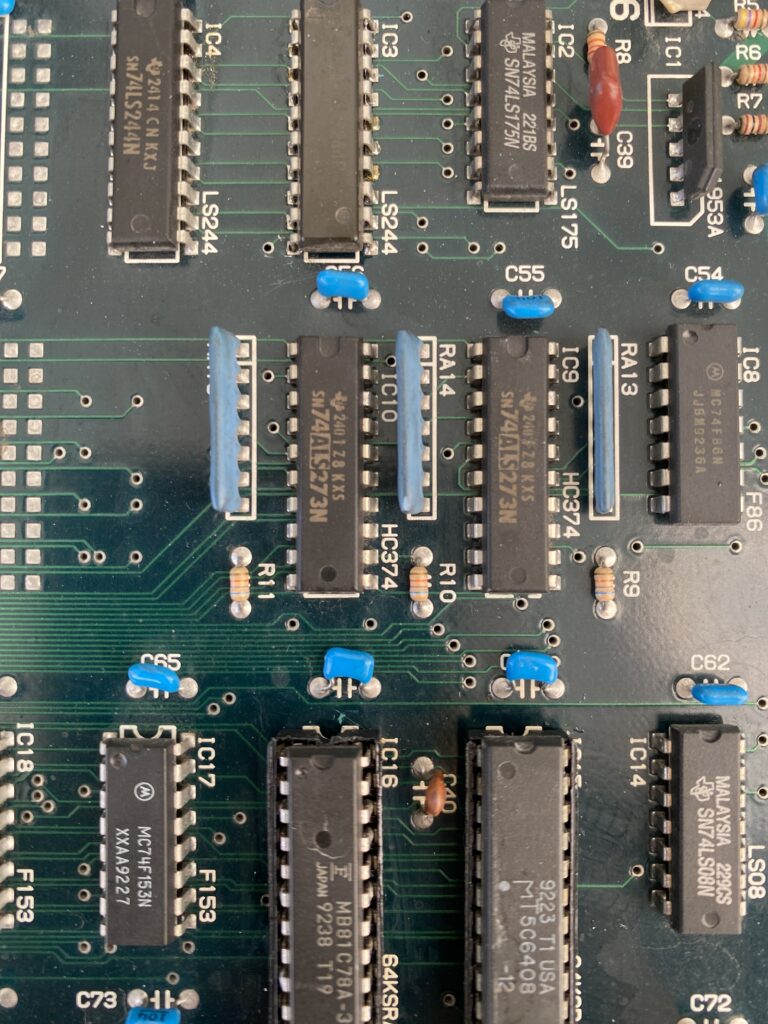
There are 3 resistor packs in this area. I measure the resistance of their feet with my multimeter – they should be equal to each other.
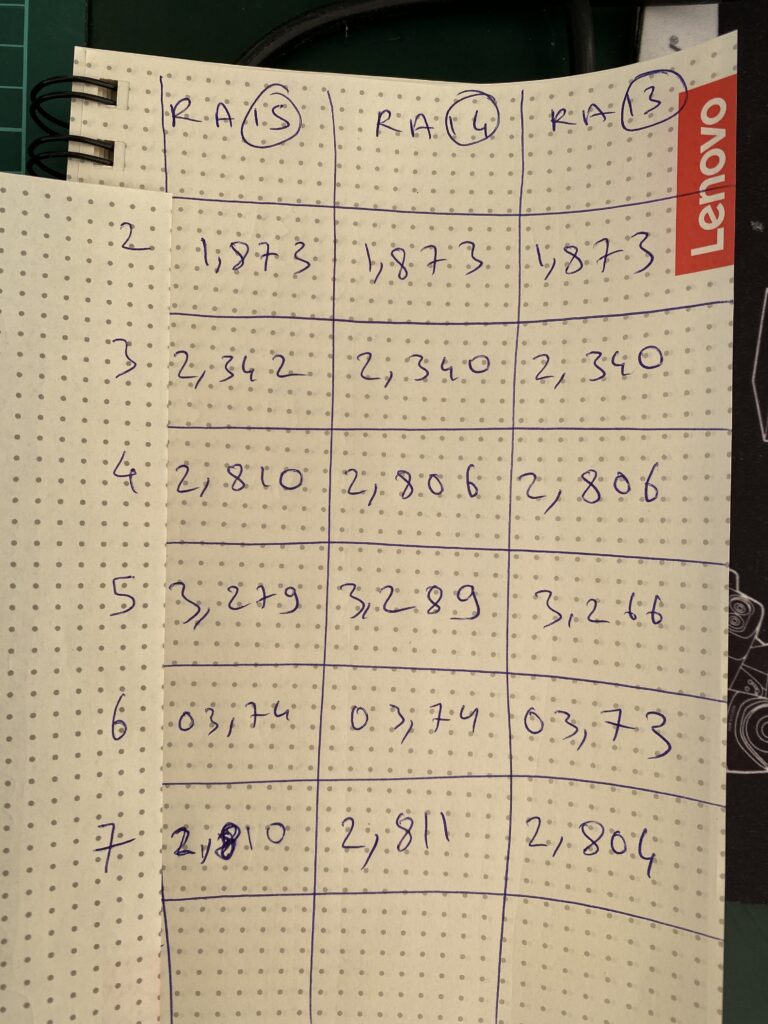
The results are good.
IC10 is a SN74ALS273N. According to the data sheet for this part, Pin 18 –> D7 (Input)
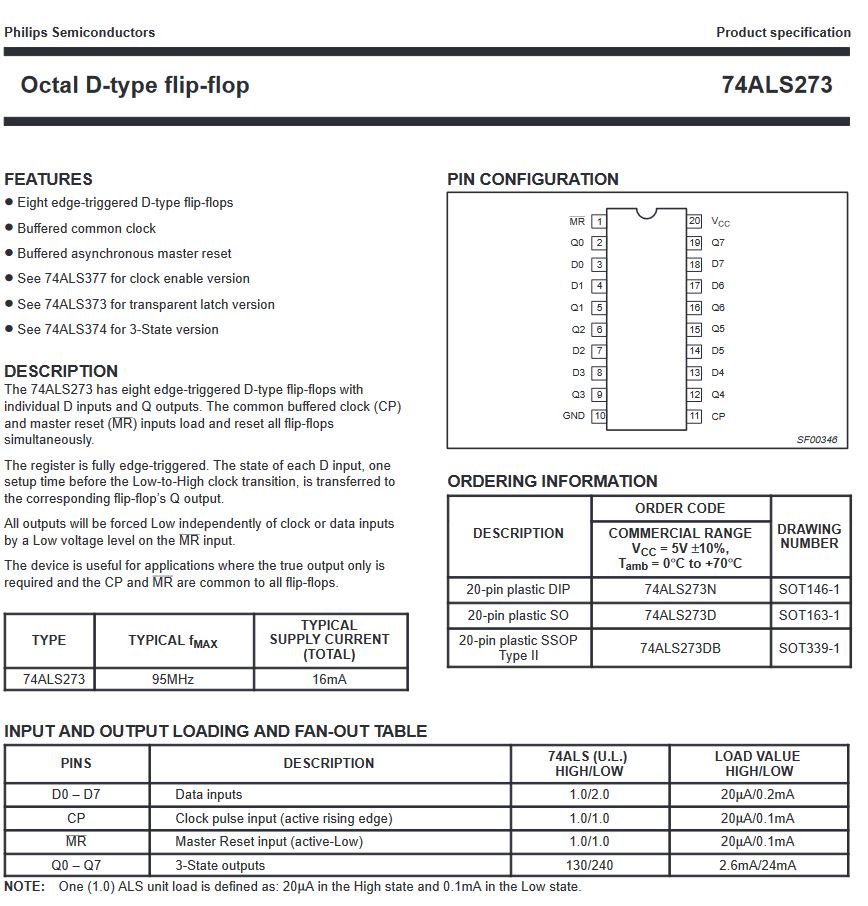
Here is my drawing of the connections between these chips:
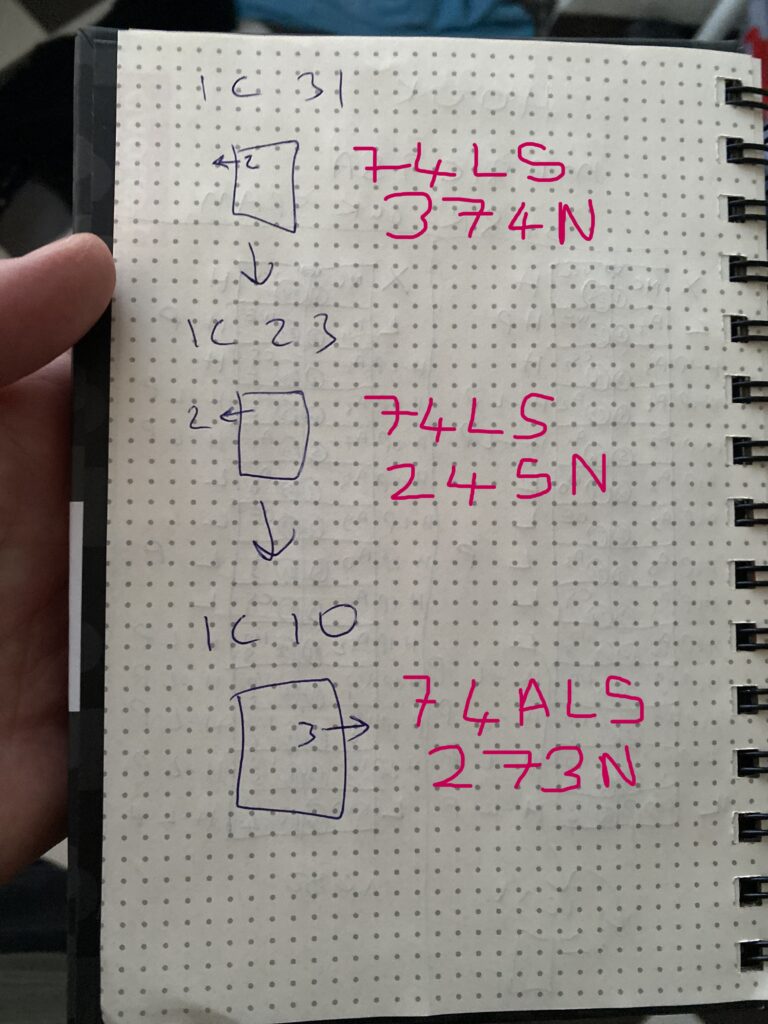
I’m thinking of replacing IC10, and then something strange catches my eye. On the chip it says SN74ALS273N but on the motherboard, HC374 is printed as the part for this chip. At first, I think that the wrong chip was installed in this board, but then I look at other photos of this board on the PLD Archive site and they are the same.
I do some research on the subject and the information I can get is that 74HC374 was used here because 74LS273 was too slow. Later, when faster 74ALS273 parts came out, they switched to them since they were cheaper.
I proceed with replacing this IC. Since I don’t have another 74ALS273 on hand, I will replace it with a 74HC374.
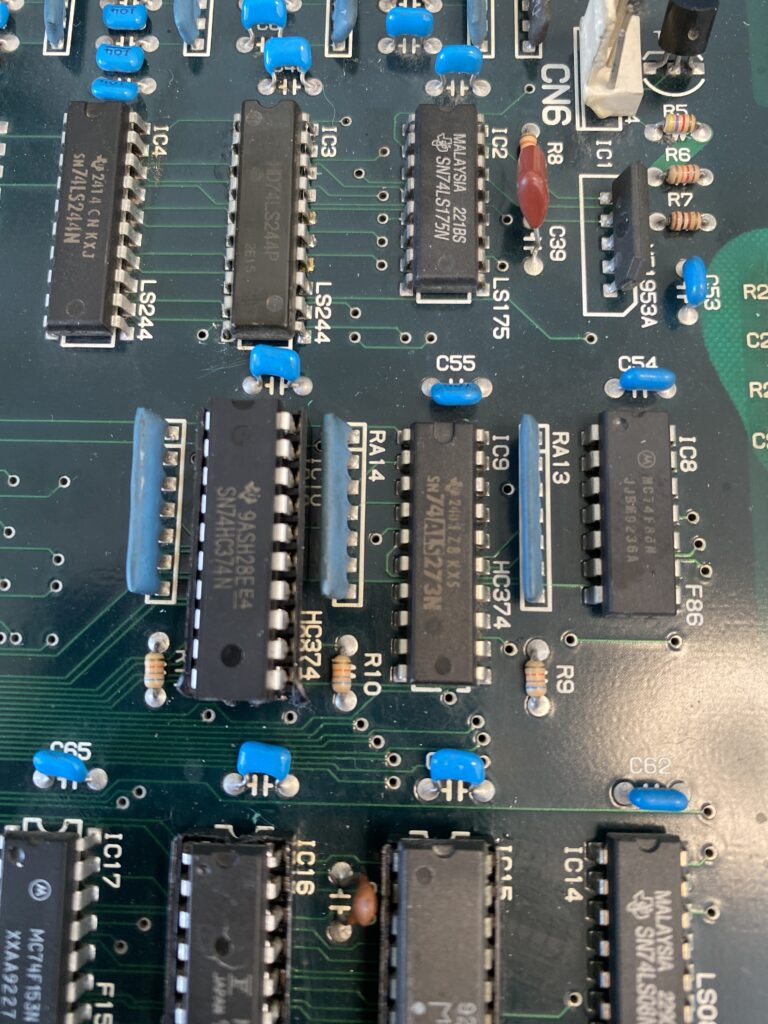
After removing the old part, I test it out of circuit in my EPROM programmer and I see that its problematic.
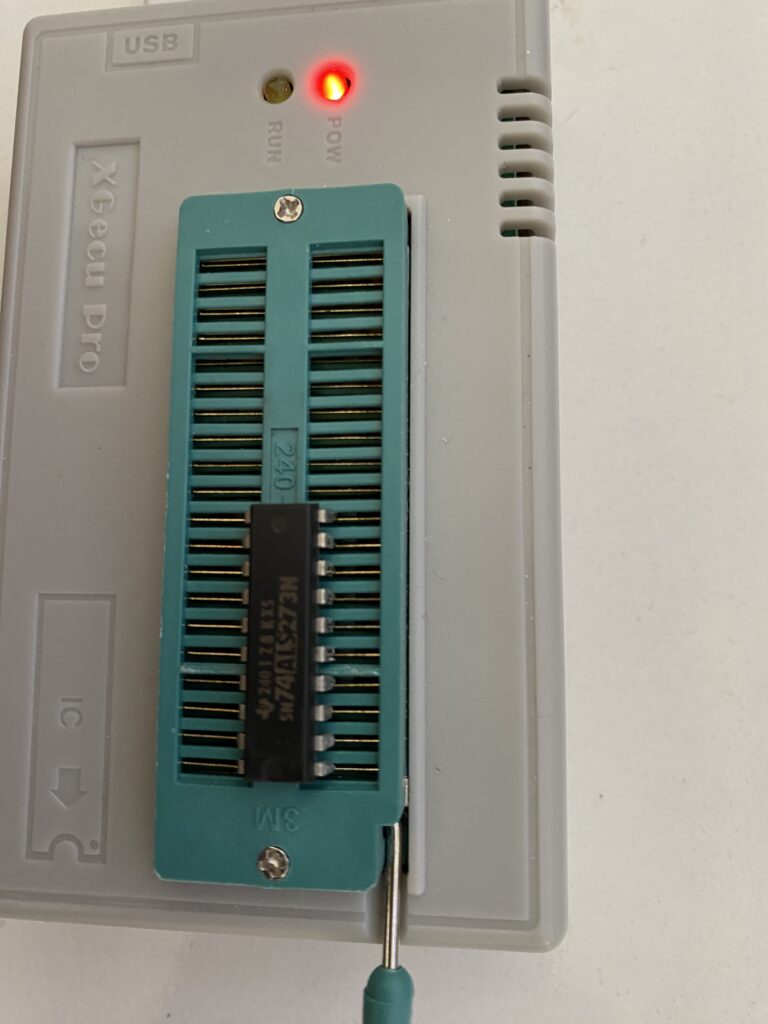
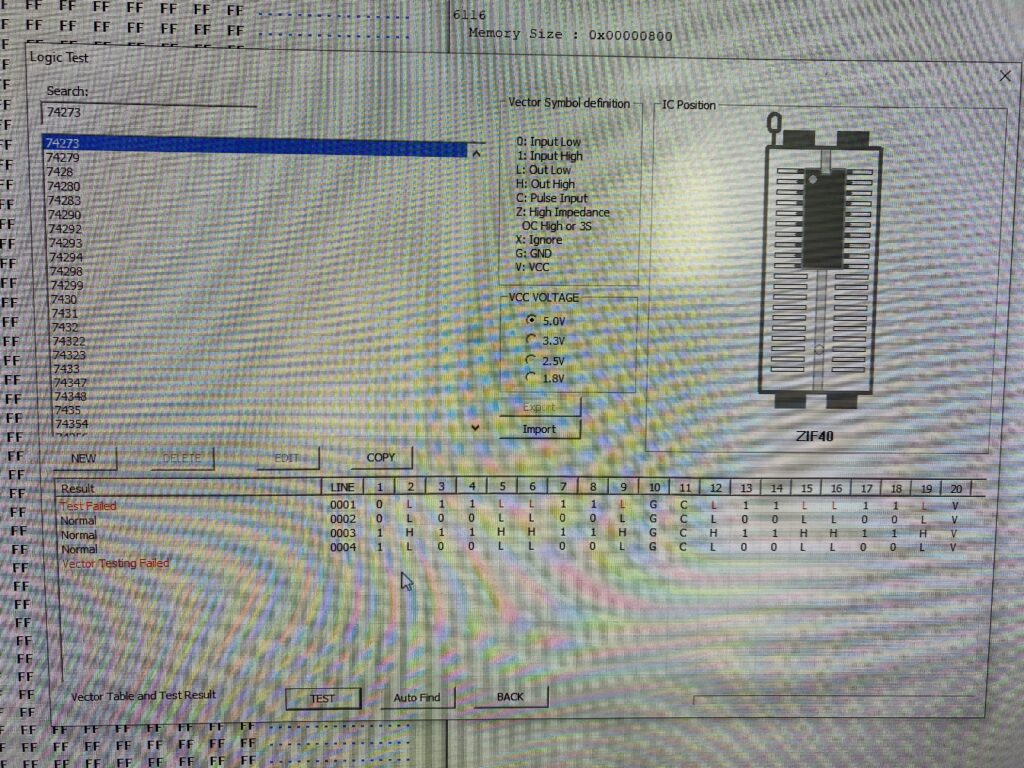
When the game now, it seems that there is a big improvement. The colors that were flickering in the background as the character walks have been fixed.
But we still don’t have red…there is only red on the far right of the screen.
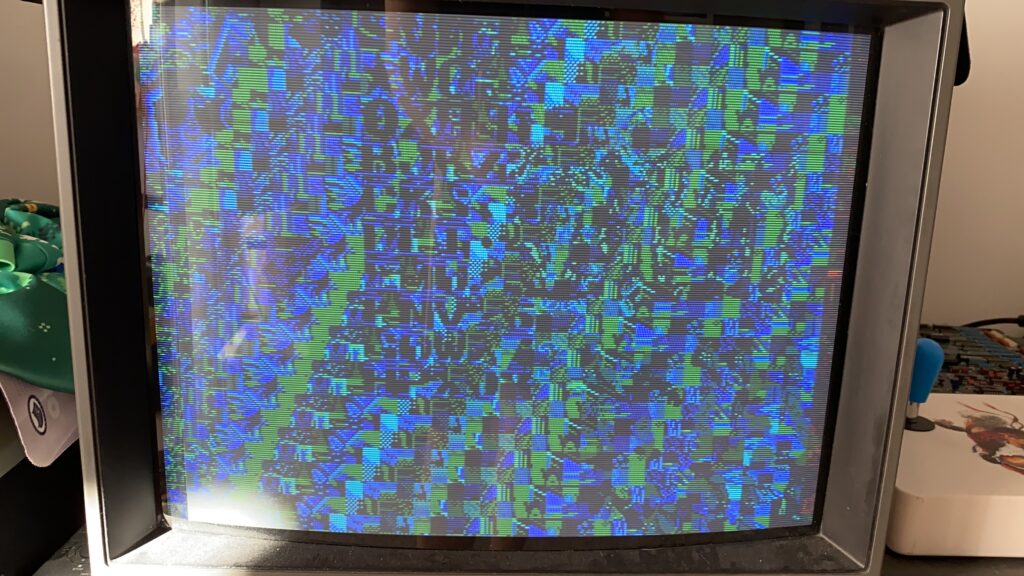
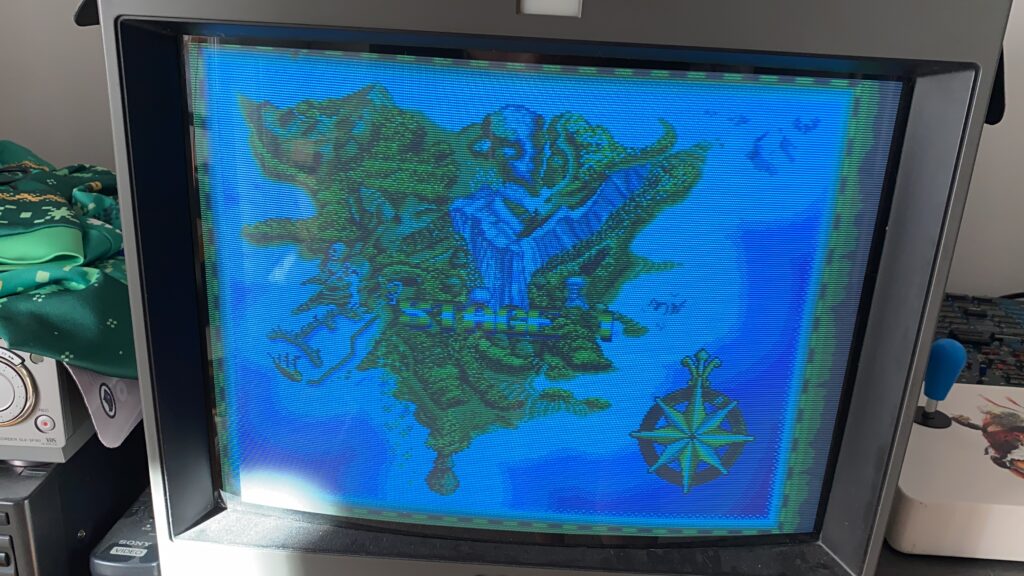
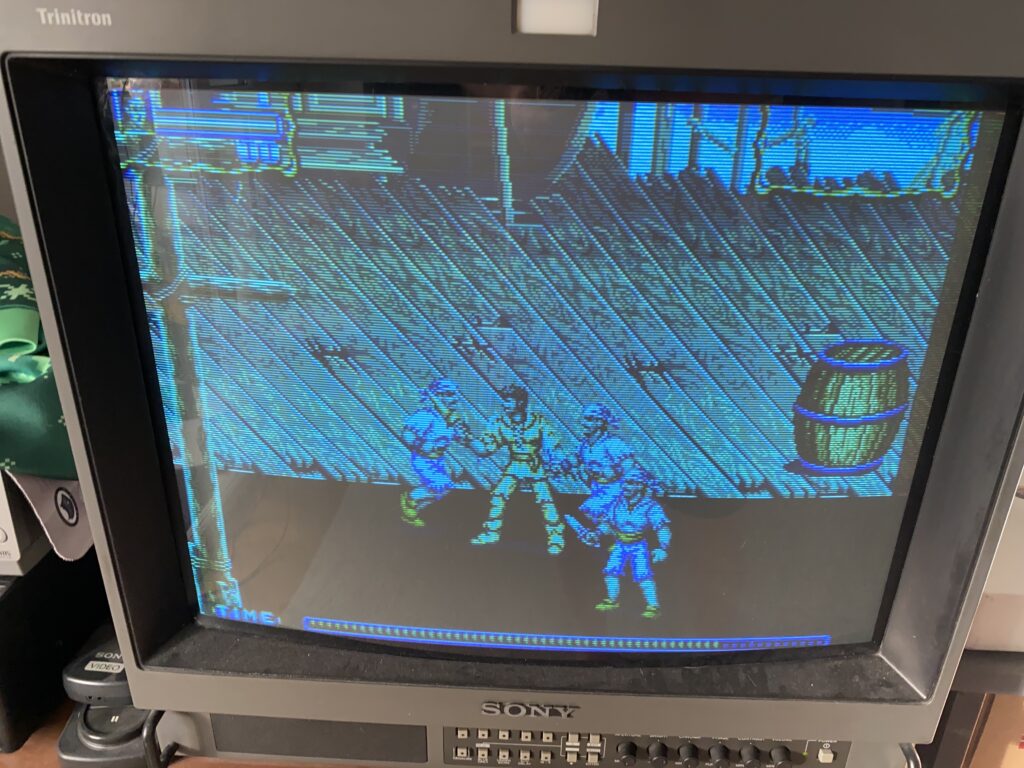
You can see it better in this video:
Let’s keep on trying. When checking the data sheets further, it seems that the pinout of this new 74HC374 IC is slightly different than the 74ALS273 it replaced.
SN74HC374N –> Pin 18 –> 8D (Input)
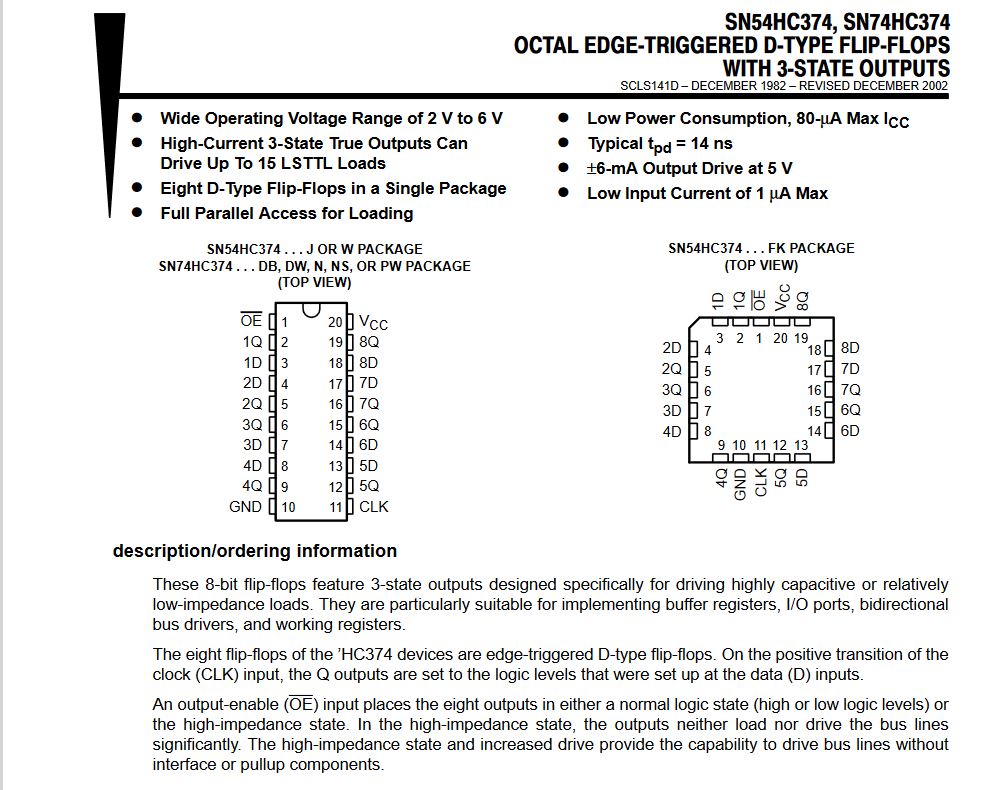
It turns out that on the 74ALS273 datasheet, the channels are numbered from 0 to 7. On the 74HC374 datasheet, the channels are numbered 1 through 8. However, the functionality between the two is the same.
I decide to remove the other 74ALS273 IC above the one I just replaced – IC9 – and test it.
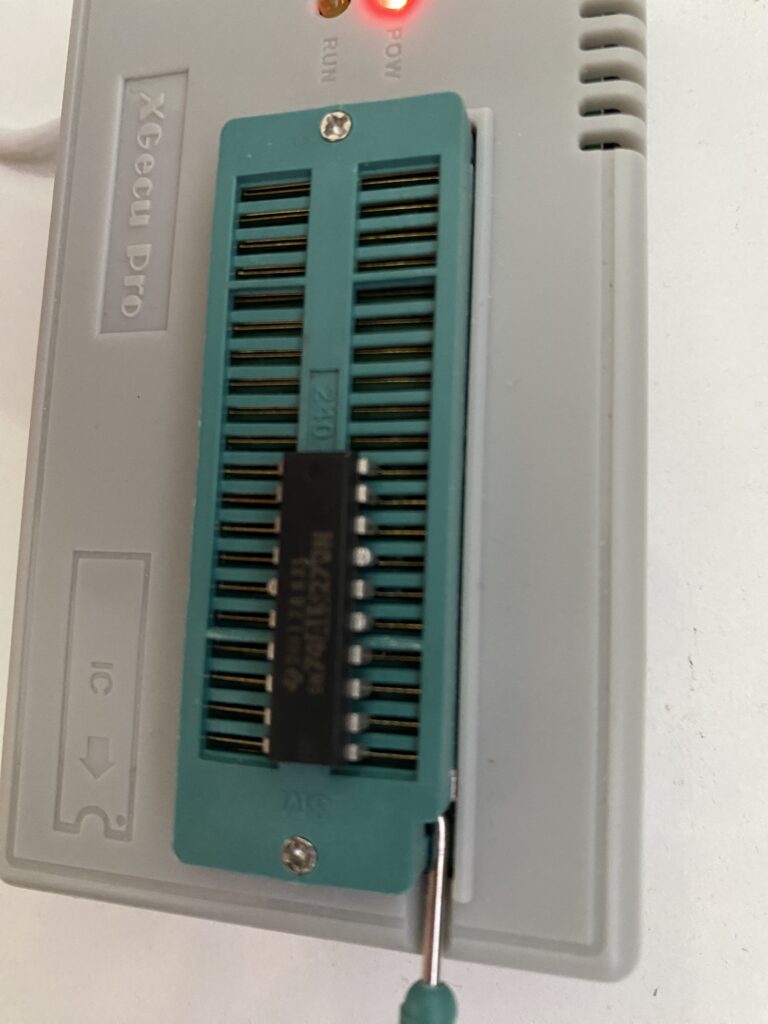
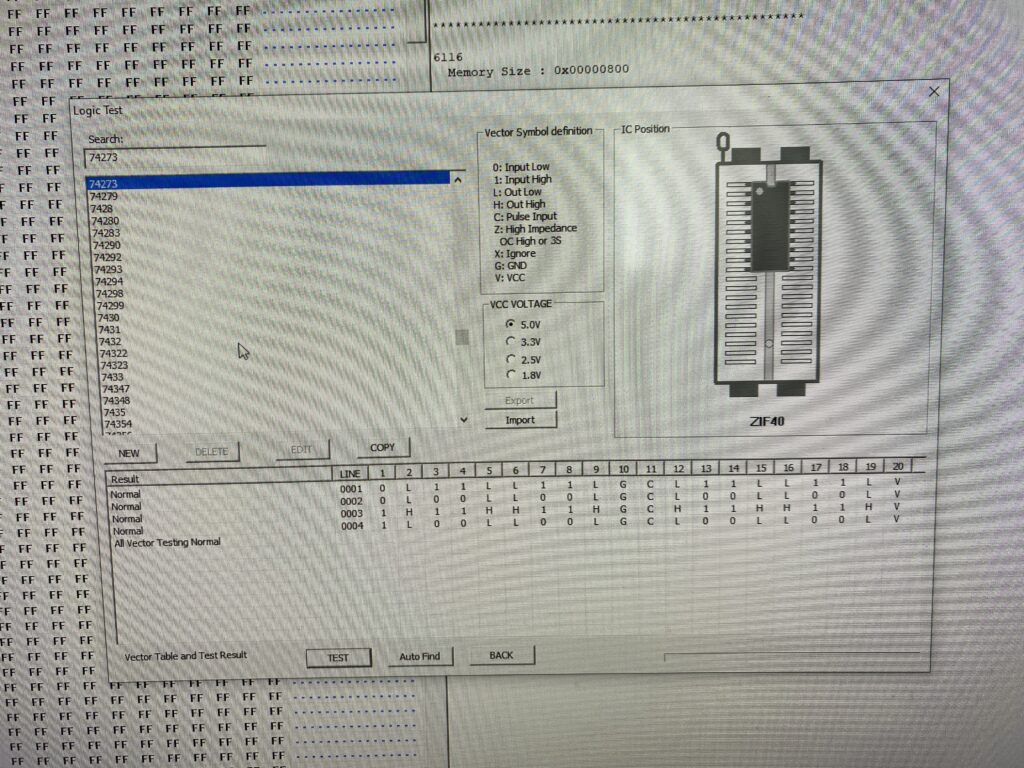
No problems in the test, but I proceed to replace it with a SN74HC374N to match IC10.
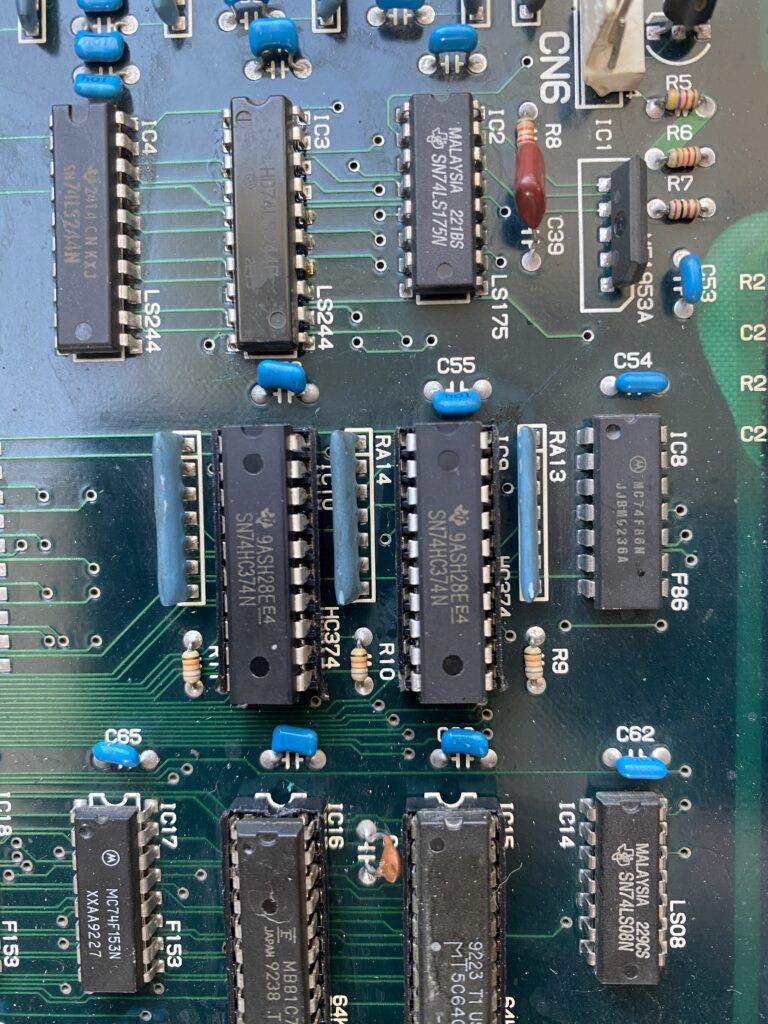
Now when powering up the board … everything works correctly. The board is saved!!!
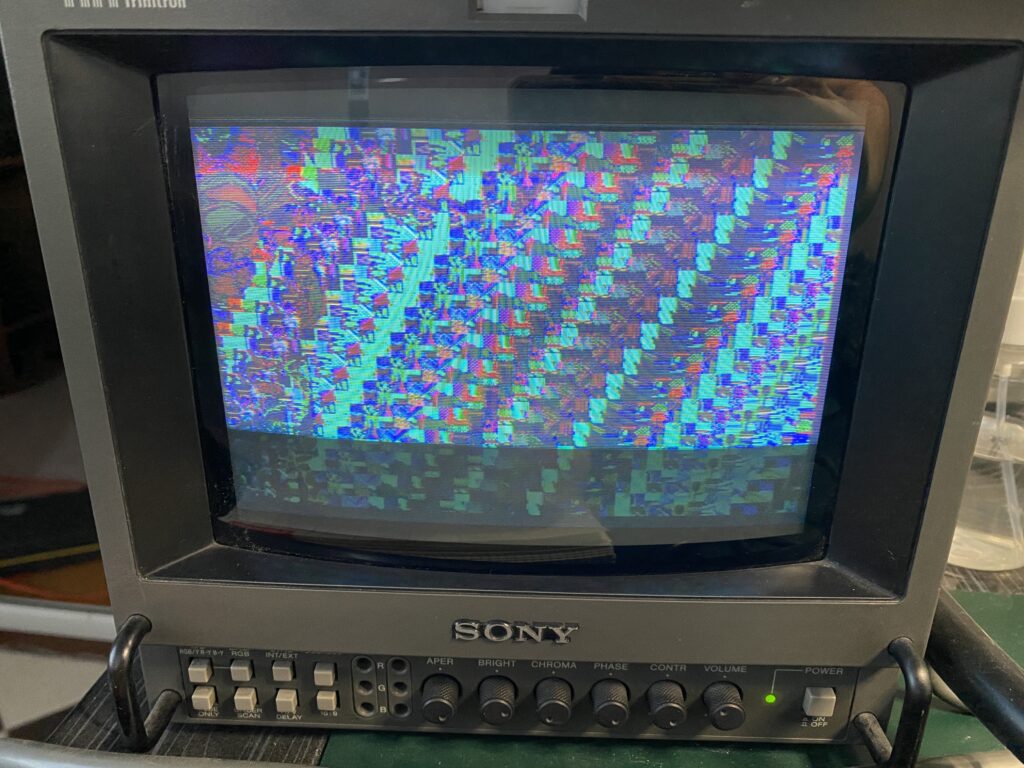
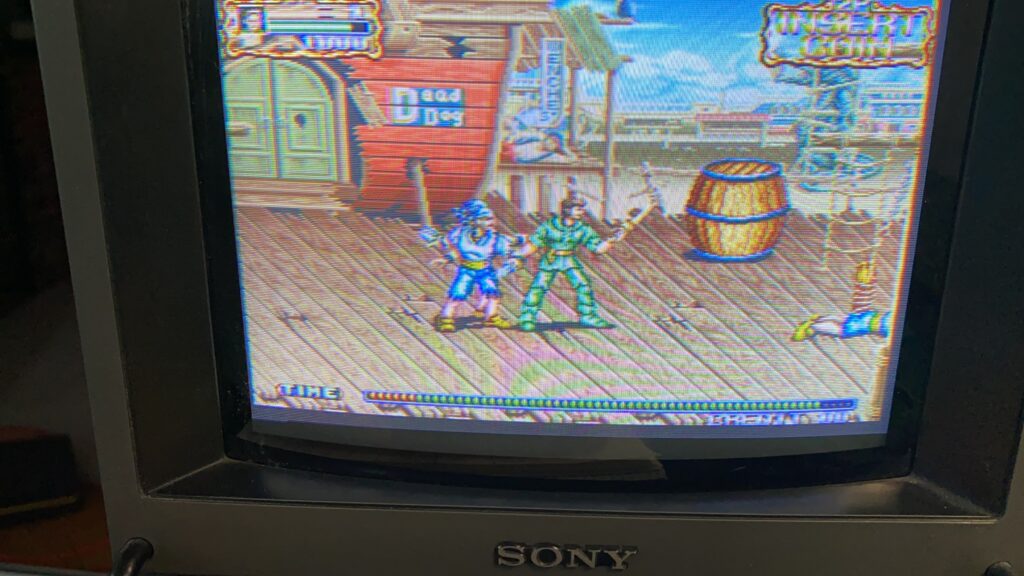
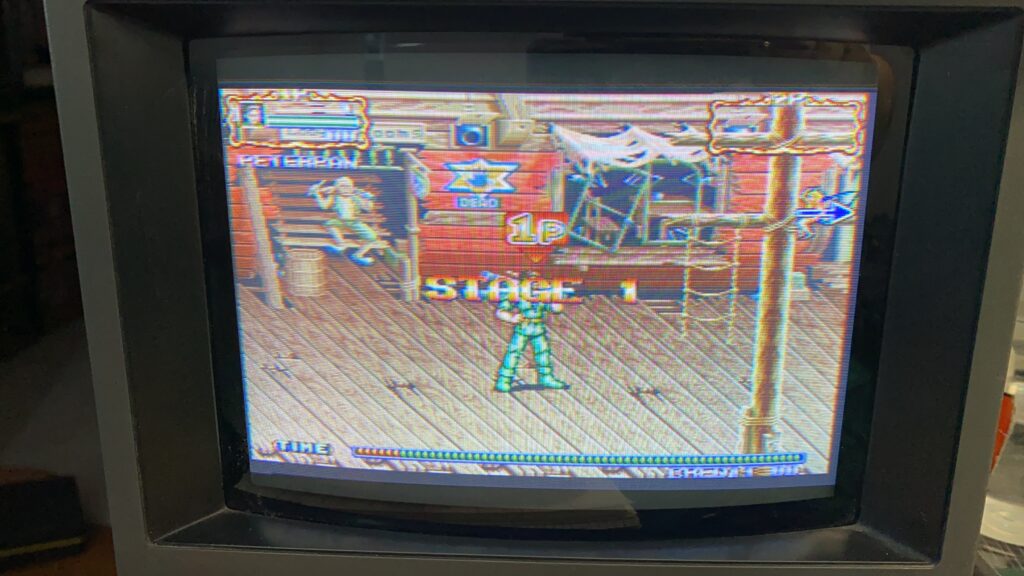
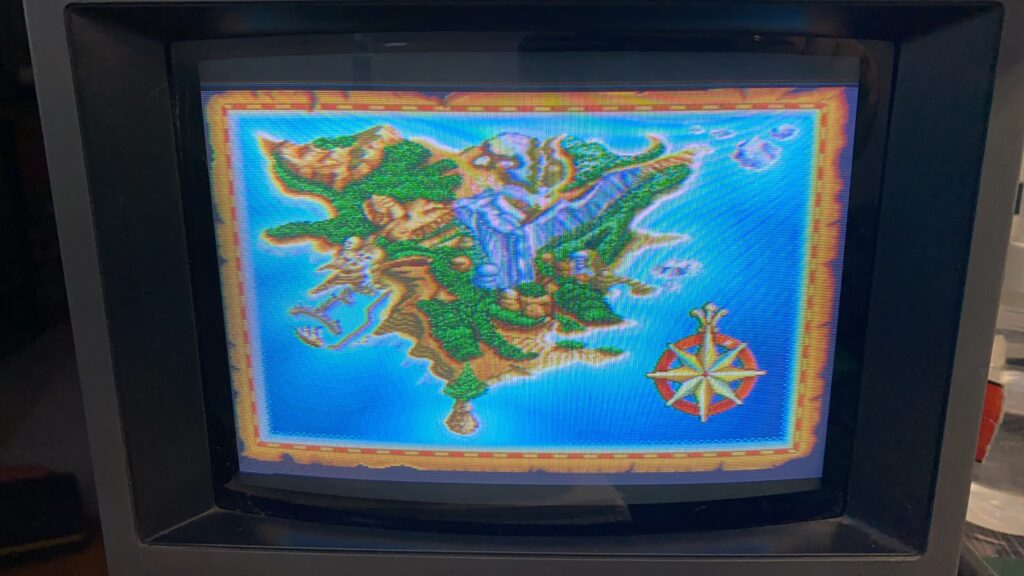
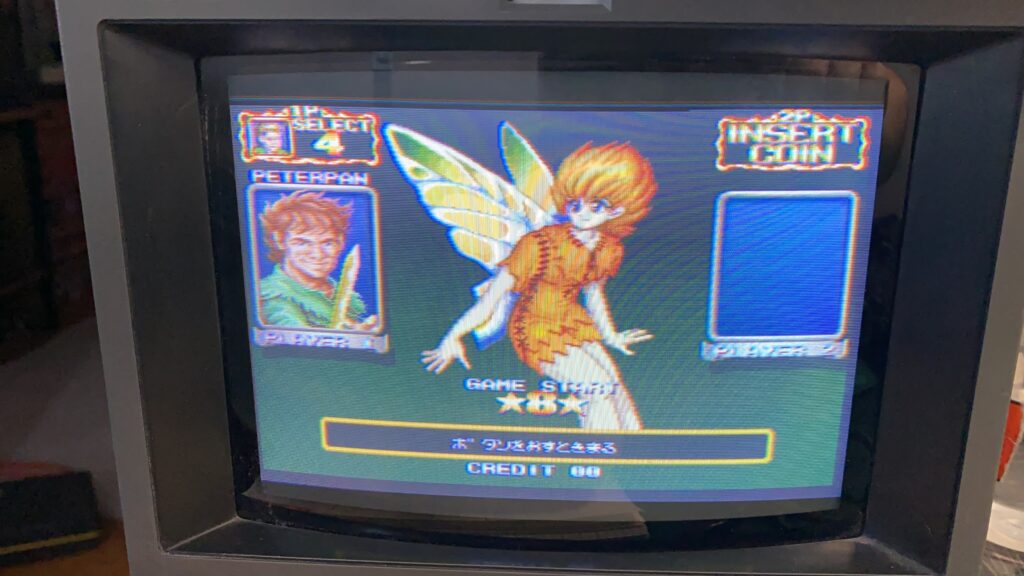
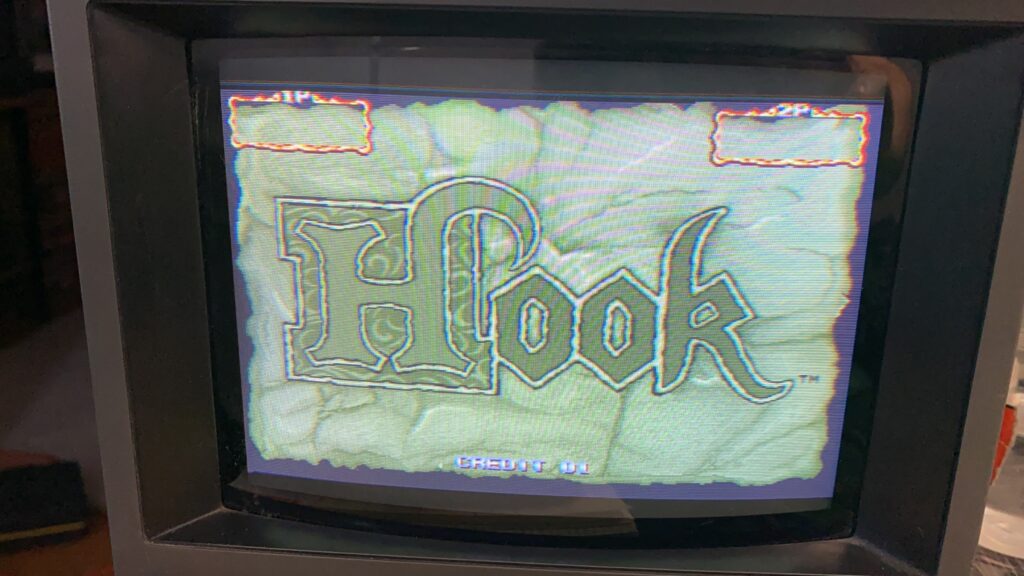
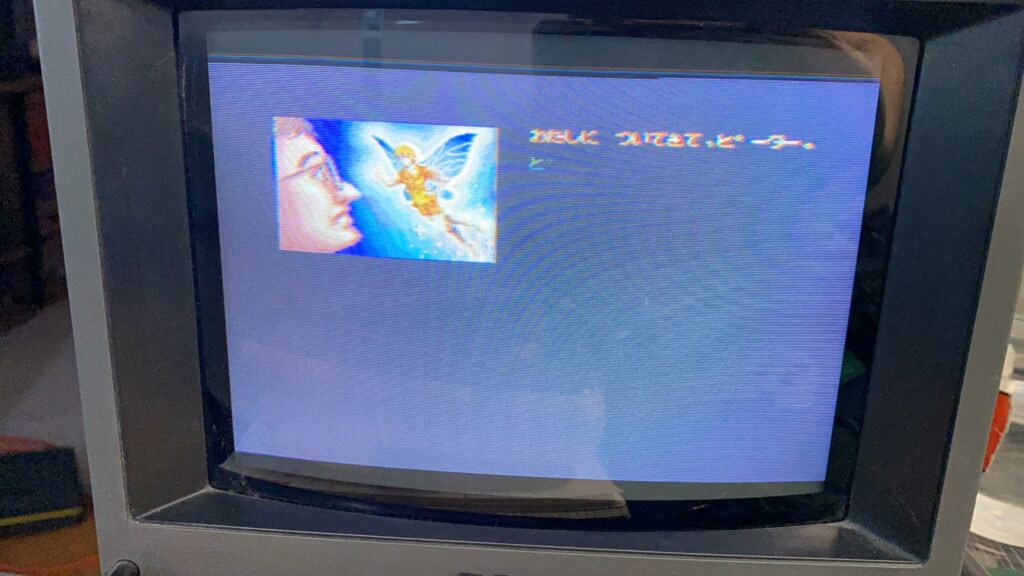
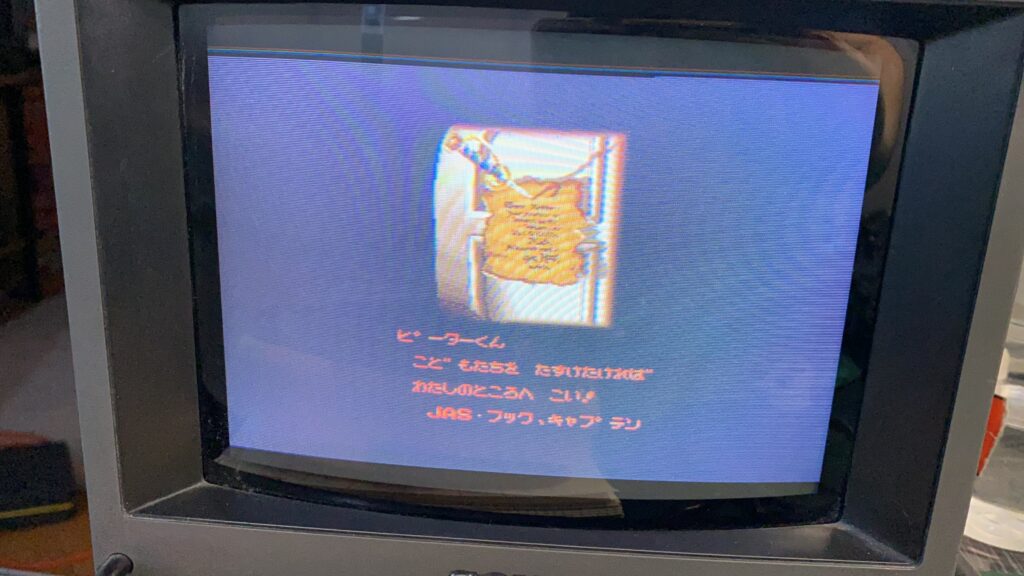
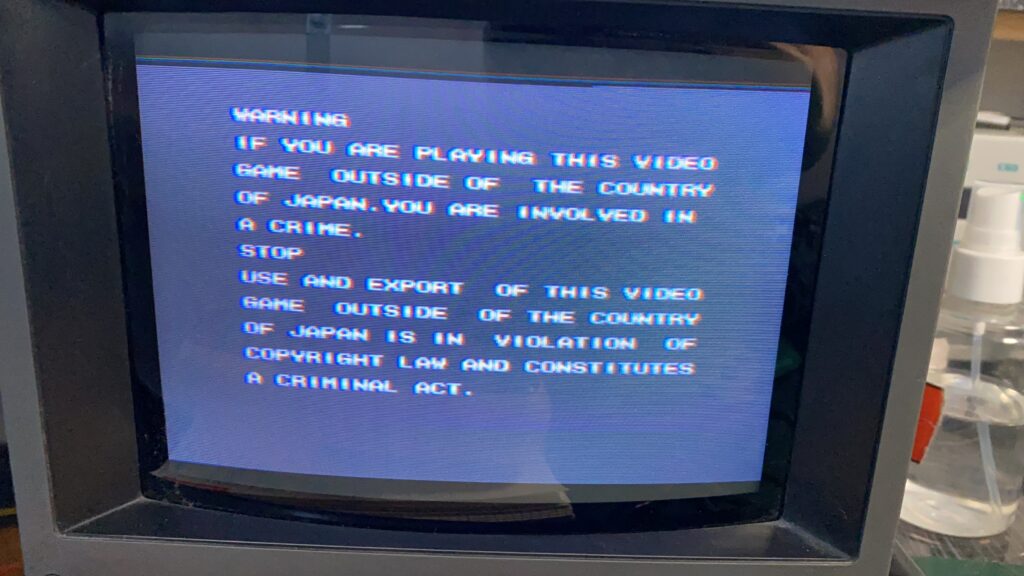
Best Regards
Oguz